Step-By-Step Window Replacement Process For Homeowners
Elisa DeFoe • June 23, 2025
Drafty rooms, rising energy bills, and windows rattling with every gust—homeowners across Denver and Northern Colorado know the signs that it’s time for an upgrade. Whether you’re battling the aftermath of one of Colorado’s legendary hailstorms, noticing stubborn leaks and warped frames, or simply hoping to boost your home’s comfort and curb appeal, replacing aging windows can make a world of difference. Not only can new, energy-efficient windows cut utility costs and keep your home cozier year-round, but they also ensure your property meets safety and egress requirements—especially important in our region’s ever-changing climate.
At Semper Fi Restoration, integrity, precision, and reliability aren’t just slogans—they’re the foundation of every project. As a veteran-owned company serving Denver and Northern Colorado, our team is dedicated to restoring homes with the discipline and attention to detail you’d expect from a Marine. Our Window Solutions service is designed to guide you from first assessment to flawless installation, with transparent communication and support at every step.
Whether you’re considering a do-it-yourself approach or weighing the benefits of professional installation, this comprehensive guide will demystify the window replacement process. From careful planning and measurement to expert removal, installation, and finishing, you’ll find clear, actionable steps to ensure your window upgrade is smooth, safe, and successful. Let’s get started on transforming your home—one window at a time.
Step 1: Plan Your Window Replacement Project and Decide Your Approach
Successful window replacements start long before the first sash comes out. A detailed plan helps you avoid ordering mistakes, unexpected expenses, and code headaches. By defining clear goals, budgeting realistically, and choosing the right installation path, you’ll save time and stress as your project moves forward.
Identify Your Goals, Budget, and Timeline
Before shopping for windows, nail down what you want to achieve and how much you can spend. Are you chasing energy savings—in some cases up to 13% on heating and cooling bills with ENERGY STAR–rated units—or fixing storm-damaged frames? Maybe you simply want a fresh look that boosts curb appeal.
Typical window replacement costs vary by scope:
- Insert (pocket) windows: $300–$600 per unit
- Full-frame replacements: $500–$1,000+ per unit
Your project timeline depends on factors like:
- Number of windows to swap
- Age and condition of your home’s framing
- Access (ground-level vs. upper floors)
- Any required permits or HOA approvals
Lay out a realistic schedule—factoring in supplier lead times and weather windows—and build in a buffer for surprises.
Decide Between DIY and Professional Installation
Tackling the job yourself can save on labor, but it demands tools, skills, and plenty of time. Consider:
- Pros of DIY: Lower labor cost, complete control over timing, personal accomplishment
- Cons of DIY: Steep learning curve, potential for warranty‐voiding mistakes, time investment
There are times when hiring a pro makes sense:
- Upper-story installs or tricky access
- Complex framing repairs
- Local code or egress requirements you’re not comfortable handling
Quick self-assessment checklist:
- Do you have the right tools (drill, shims, flashing tape, caulk guns)?
- Have you replaced windows before or spent time on carpentry projects?
- Can you devote full days (or weekends) to demo, install, and cleanup?
If you answered “no” to more than one question, a seasoned installer will likely save you headaches in the long run.
Factor in Insurance Claims and Financing Options
In Colorado, unexpected hail and windstorms can leave windows cracked or frames dented. Filing a timely insurance claim can cover a large portion of the repair or replacement cost—but the process often feels like navigating an obstacle course.
Semper Fi Restoration takes the guesswork out of insurance coordination. We’ll document damage, work with your adjuster, and ensure your claim accurately reflects the scope of needed repairs—for both roofs and windows.
When it comes to payment, you have options:
- Flexible in-house financing or payment plans
- Home-equity loans or lines of credit
- Bundling window work with other exterior projects for volume discounts
Mapping out your claim strategy and financing choice early on keeps your project moving—and your budget intact.
Step 2: Schedule a Professional Consultation and Assess Existing Windows
Before you pull out the tape measure or order replacement sashes, it pays to have an expert eye survey your existing windows. A thorough inspection reveals issues you might miss—rotted jambs hidden behind trim, water intrusion seeping into cavities, or windows that no longer meet egress requirements for bedrooms and basements. Scheduling a professional consultation not only pinpoints these trouble spots but also gives you a clear picture of what your replacement project will involve.
When you book an assessment, Semper Fi Restoration’s team brings the same military-grade attention to detail they apply to roofing and other exterior work. You’ll walk through the project timeline and share your goals, then leave the technical evaluation to specialists equipped with thermal imagers, moisture meters, and code checklists. Armed with their report, you’ll have an accurate scope of work, realistic budget estimates, and confidence that no hidden defect will derail your window replacement process.
Book a Free Window Assessment with Semper Fi Restoration
To get started, head to Semper Fi’s Window Solutions page and request your complimentary inspection. A project coordinator will confirm the date and walk you through any preparatory steps. On assessment day, a trained technician will:
- Perform draft testing around frames and sashes
- Scan for cold or hot spots with thermal imaging
- Inspect framing for rot, decay, or insect damage
- Measure window dimensions and verify egress compliance
All findings are consolidated into a digital report, complete with photos and prioritized recommendations.
Document Existing Conditions and Take Preliminary Notes
While the pros are on site, you can help by photographing each window—inside and out—and making quick notes. Use this checklist to guide your observations:
- Warped or bowed window frames
- Failed seals or foggy panes
- Evidence of water stains or rot on sills and jambs
- Cracked glazing or broken weatherstripping
- Egress openings that fall short of code (net clear area under 5.7 sq ft)
Your photos will serve as a handy reference when you compare before-and-after results or discuss insurance claims.
Review Warranty, Service, and Post-Install Support Options
A quality installation is only as good as its follow-through. Semper Fi Restoration stands behind its work with robust workmanship guarantees, clear communication channels, and scheduled follow-up inspections. After installation, you’ll receive:
- A detailed record of all repairs and replacements
- Guidance on seasonal maintenance and inspections
- Access to maintenance packages covering caulk resealing, hardware lubrication, and window cleaning
With service that extends beyond the final nail, you can rest easy knowing your new windows will perform as promised for years to come.
Step 3: Choose Replacement Window Type, Material, and Energy Efficiency
Replacing windows isn’t just a matter of swapping glass—it’s choosing the right system for your home’s structure, your budget, and Colorado’s wild temperature swings. In this step, you’ll compare insert versus full-frame options, weigh material choices, and zero in on energy ratings that make sense for Denver and Northern Colorado.
Understand Insert (Pocket) vs. Full-Frame Replacement
Insert (pocket) windows slide into your existing frames, making them the go-to for homes with sound, square openings. If your windows show minimal rot, no major framing damage, and you’re happy with the current rough-opening size, inserts can save time and money—typically costing between $300 and $600 per unit. Imagine a 1950s ranch where the original frames are solid and uniform: a pocket replacement refreshes the look without disturbing interior trim or exterior siding.
Full-frame replacements replace the entire unit—frame, sash, and all. They’re essential when sills are rotted or you want to slightly adjust opening dimensions. While they run higher (often $500 to $1,000+ per window), you get a brand-new substrate, better insulation continuity, and flexibility to swap styles—ideal for a modern build or a remodel where the old frame’s integrity is beyond repair.
Compare Window Materials and Styles
Once you’ve picked your installation type, material choice is next. Here’s how common options stack up:
Material | Insulation Value (R-Value) | Maintenance | Lifespan | Cost Range* | Aesthetic Fit |
---|---|---|---|---|---|
Vinyl | 3.0–4.0 | Clean with soap & water | 20–30 years | $300–$700 | Clean lines, versatile |
Wood | 2.8–3.5 | Annual painting/staining | 20–40 years | $600–$1,200 | Traditional, warm tones |
Fiberglass | 4.0–5.0 | Minimal (occasional wash) | 30–50 years | $700–$1,500 | Modern or historic |
Aluminum-clad | 3.5–4.5 | Low (occasional wash) | 30+ years | $800–$1,600 | Contemporary, sleek |
*Costs per window, installed; vary by size and region.
- Vinyl offers great value and low upkeep, popular in suburban homes.
- Wood brings classic character, but you’ll repaint or restain periodically.
- Fiberglass handles extreme temperature swings with minimal expansion and contraction—an excellent match for Colorado’s freeze-thaw cycles.
- Aluminum-clad combines a wood interior with a durable metal exterior, balancing looks and resilience.
Select ENERGY STAR-Certified Windows for Your Climate Zone
An easy way to lock in long-term savings and comfort is to choose windows that meet ENERGY STAR performance requirements for our climate zone. Two key metrics:
- U-Factor: Measures heat loss. Look for ≤ 0.30 in Denver and Northern Colorado.
- Solar Heat Gain Coefficient (SHGC): Indicates how much solar radiation passes through. Aim for 0.25–0.30 to balance winter warmth and summer shade.
Windows certified for Zone 5 (our zone) can cut your heating and cooling bills by up to 13% compared with non-rated windows. When comparing products, always double-check the NFRC label for exact U-Factor and SHGC numbers. That way, you get a window that keeps Colorado’s sunshine and storms out where they belong—outside.
Step 4: Measure Existing Windows for Accurate Ordering
Accurate measurements are the key to seamless window ordering and installation. Mistakes here can lead to ill-fitting units, frustrating delays, and extra costs. By taking precise dimensions and noting frame irregularities, you’ll ensure your new windows fit like a glove—no guesswork required.
Gather Measurement Tools and Prepare to Record Data
Before you start, assemble everything you need to capture dimensions cleanly:
- 25-foot tape measure
- Carpenter’s level for checking plumb and level
- Framing square to verify right angles
- Sharp pencil and sturdy notebook
- Camera or smartphone for quick reference photos
Choose a calm day with good natural light so shadows don’t obscure edges, and you can read numbers clearly. Lay out your tools on a drop cloth or table near the work area so nothing wanders off.
Measure Width, Height, and Depth in Three Locations
To account for settling, warping, or slight framing shifts, measure each dimension in three spots and note the smallest figure:
- Width: Measure inside the jamb at the top, middle, and bottom of the opening.
- Height: Measure from the sill to the head jamb at the left, center, and right sides.
- Depth: Measure the jamb thickness from the interior stop to the exterior stop or brickmould.
Record each trio of measurements in your notebook, then circle the smallest width and height—those determine your replacement size. If diagonal measurements vary by more than 1/4 inch, the opening is out of square; jot down those diagonal lengths and plan for shims or frame adjustments.
Communicate Measurements to Supplier and Confirm Fit
Once your numbers are on paper, double-check them against the manufacturer’s specs—particularly whether they list rough-opening dimensions versus finish-opening (brickmould) sizes. It’s all too common to mix up the two. As a precaution, consider ordering a single sample window first. Test-fitting that unit in your rough opening lets you catch any sizing quirks before the full shipment arrives. With precise measurements and a smart fit test under your belt, you can move ahead confidently, knowing your new windows will arrive ready for a smooth install.
Step 5: Prepare Your Home and Work Area for Safe Installation
Before any windows come out or new frames go in, it’s crucial to set up a protected, well-organized workspace. Taking time to clear treatments, shield your floors and furniture, and assemble the right tools will keep your home intact, speed up the installation, and reduce the risk of accidents. Whether you’re rolling up your sleeves or welcoming a professional crew, these prep steps lay the groundwork for a smooth, damage-free project.
Remove Window Treatments, Décor, and Hardware
Begin by stripping each window of everything that might get in the way—or get damaged—during installation.
- Take down blinds, shades, curtains, and drapery rods.
- Remove decorative valances, stained-glass inserts, or peel-and-stick privacy films.
- Unscrew any hardware you plan to reuse, like tension rods or lock kits, and stash the screws and brackets in labeled, sealed bags.
- Slide screens out of their tracks and stack them safely in a corner.
Labeling each bag with the window’s location (e.g., “Living Room – North Wall”) will speed up reassembly and ensure nothing goes missing.
Protect Interiors and Manage Access Points
With window treatments gone, it’s time to shield your home’s interior and plan clear entry paths for installers:
- Lay down heavy-duty canvas drop cloths or plastic sheeting over floors, furniture, and nearby surfaces. Fasten edges with painter’s tape so they don’t shift.
- Push sofas, tables, and knick-knacks well back from each opening to give workers room to maneuver.
- If children or pets will be underfoot, arrange a safe zone away from the work area—this isn’t the time for curious paws or little fingers.
- Keep a clear line of sight and an unobstructed path to each window; installers often need interior access to check for level, plumb, and insulation placement.
A tidy, hazard-free zone not only protects your belongings but also lets the crew—or you—work more quickly and confidently.
Gather All Required Tools and Materials
Having every tool at arm’s reach eliminates frantic trips to the garage or hardware store mid-project. Here’s a starter checklist for a typical window replacement:
- Drill/driver and a set of bits
- Oscillating multi-tool for trim and stop removal
- Pry bar and putty knife
- Carpenter’s level and a framing square
- Assorted wood shims
- Self-adhesive flashing tape
- Silicone caulk (exterior-grade) and paintable latex caulk (interior)
- Low-expansion spray foam insulation
- Foam-rubber backer rod for larger gaps
- Wood filler or epoxy patch material
- Utility knife with fresh blades
- Safety glasses, work gloves, and dust masks
- Canvas drop cloths or heavy plastic sheeting
With these essentials in place, you’ll be ready to tackle the next phase—pulling out old windows and prepping the rough opening—without missing a beat.
Step 6: Remove the Existing Windows and Frames
Before installing new windows, you’ll need to carefully take out the old units—including any storm sashes, trim, stops, and weights—while preserving the surrounding structure. This step requires patience and the right tools to avoid damaging siding or interior finishes. If your home was built before 1978, be mindful of potential lead paint; if you suspect lead, consider hiring a certified abatement professional to handle the removal safely.
Remove Storm Windows and Exterior Trim
Start on the outside by stripping away any storm or security windows. Use a utility knife to score along paint lines where the storm frame meets the house, then remove screws or sliding clips that hold the units in place. A putty knife or a 5-in-1 multi-tool will help pry off stubborn pieces without gouging the siding.
Next, label each trim piece with its window location (for example, “Bedroom East Wall – Top Trim”) and gently pry it free. Slide the tool between the trim and the sheathing, working your way along the edges to break any paint seal. Store reusable trim in a dry spot—properly labeled and stacked—to simplify reinstallation later on.
Detach Sashes, Stops, Weights, or Springs
With exterior trim out of the way, turn your attention inside (for full-frame replacements, you may need to access interior stops first). Remove the appropriate stops—interior or exterior—depending on which side you’re working from. Always score paint lines first, then use a pry bar or putty knife to ease the stops off without cracking.
Older double-hung windows often have counterweights or spiral springs. If you encounter weights on a cord, carefully cut the cord near the top and let the weight drop into the pocket. For spring-balance systems, locate and unscrew the jamb brackets, then gently release tension. Wear eye protection—these components can snap unexpectedly. Label and store weights or springs in sealed bags to keep them out of the way.
Clear Out and Repair the Frame
Once the sash and hardware are removed, clean out the rough opening. Scrape away leftover glazing, old caulk, and debris. Inspect the sill plate and jambs for soft spots or rot. Small holes and cracks can be filled with a high-quality wood filler or epoxy patch, but any severely decayed sections should be cut out and replaced with new, treated lumber.
Make sure the repaired area provides solid backing for your new window fasteners. Reinforce questionable sections by “sistering” a matching board alongside the existing framing, using exterior-grade wood glue and corrosion-resistant screws. A sturdy, level substrate will help ensure your new window sits square and operates smoothly for years to come.
Step 7: Inspect the Rough Opening and Ensure Building Code Compliance
Before slipping in a new window, take a moment to evaluate the rough opening itself. A plumb, level, and square opening not only ensures smooth operation and a tight seal but also protects you from future issues like water infiltration, air leaks, or structural wear. And because building codes set specific requirements—especially for bedroom egress and below-grade windows—you’ll want to tackle compliance at this stage to prevent safety hazards and inspection delays.
Check for Level, Plumb, and Square
Use a long carpenter’s level to verify that the sill is perfectly horizontal and each side jamb is perfectly vertical. Next, press your framing square into each corner to confirm true right angles. Finally, measure the diagonals from corner to corner; they should match within 1/8 inch. If the opening is out of tolerance, plan to correct it with strategically placed shims or by straightening the framing before you proceed.
Repair or Reinforce Damaged Framing
Inspect the sill plate, king studs, and jack studs for rot, cracks, or warping. Small holes and splits can be filled with an exterior-grade epoxy wood filler, but any compromised member should be replaced or sistered. To sister, cut a pressure-treated board to match the length of the damaged stud or sill, apply a bead of high-bond exterior adhesive, clamp it in place, and drive 3- to 4-inch corrosion-resistant screws through both layers. This reinforcement restores the opening’s structural integrity and provides a solid substrate for your new window flange or nail fin.
Confirm Emergency Egress Requirements
If this window serves a bedroom, basement or any space requiring an emergency exit, verify that it meets the International Residential Code’s egress standards. According to the ICC egress specifications :
- Net clear opening of at least 5.7 sq ft (ground floor) or 5.0 sq ft (basement)
- Minimum clear width of 24 inches and clear height of 20 inches
- Window wells (for below-grade installations) offering at least 9 sq ft of floor area, with a minimum horizontal dimension of 36 inches—and a permanent ladder or steps if deeper than 44 inches
Addressing these checks now ensures your replacement window will function flawlessly, seal out the elements, and keep your home safe and code-compliant for years to come.
Step 8: Install the New Replacement Windows
Before you break out the screws or lift that new sash into place, review the chosen installation type—insert or full-frame—and gather any manufacturer-specific instructions. Taking it slow and methodical here pays dividends in long-term performance. Whether you’re updating a snug, undisturbed pocket frame or inserting a brand-new full surround, these steps will help you achieve a tight fit, smooth operation, and a clean finish.
Installing Pocket (Insert) Windows
Pocket windows fit neatly into your existing frame, leaving interior trim and exterior siding intact. Follow these essentials:
-
Apply a Continuous Bead of Caulk
Along the interior stops or blind stops, lay a 3/8″ bead of high-quality silicone or polyurethane caulk. This sealant fills minor gaps and provides a moisture barrier against drafts and water intrusion. -
Dry-Fit the Unit
Carefully lift the window into the opening, resting it on the sill. Check that the frame sits squarely, leaving a consistent ¼″ to ⅜″ gap around the perimeter. Remove the unit once you’ve confirmed the fit. -
Position Shims and Secure
Slide the window back in place. Place wood or composite shims at each factory-drilled screw location in the frame. Push the window firmly against the interior stops, then drive screws through the pre-drilled holes and shims, fastening the frame lightly. Avoid overtightening—your goal is to hold everything plumb without bowing the frame. -
Check Operation and Finalize
Open and close the sash to confirm a smooth glide. If the window binds or sticks, adjust shims behind the jambs and at the sill until the sash moves freely. Trim any shim excess flush with a utility knife once you’re satisfied with the alignment.
Installing Full-Frame Replacement Windows
Full-frame replacements require removing your old assembly completely and setting a new frame into the rough opening. Accuracy here is key:
-
Set the Window in Place
Lift the new unit—complete with nail fin or integral flange—into the rough opening from the outside. The flange should sit flush against the sheathing or house wrap, creating the first weather barrier. -
Shim Head, Jambs, and Sill
With the window temporarily held in place, insert shims at the head jamb, each side jamb, and the sill’s corners. Check for level, plumb, and square, using your level and framing square. Tap shims gently with a hammer until the window is perfectly aligned. -
Fasten Per Manufacturer’s Pattern
Drive corrosion-resistant nails or screws through the flange at the recommended spacing—typically every 12″ to 16″ along the head and jambs. Begin loosely so you can tweak adjustments, then tighten once you’ve re-verified level and plumb. -
Re-Check and Adjust
After initial fastening, test the window’s operation. Look for even reveal around all four sides and ensure the sash (or operable panel) glides without resistance. Add or reposition shims, then finish tightening fasteners to lock everything in place.
By following these targeted steps for insert or full-frame installations, you’ll create a solid, secure base for the flashing, insulation, sealing, and trim work that follow. Next up, we’ll walk through proper flashing and sealing to protect your new windows against Colorado’s moisture and temperature swings.
Step 9: Flash, Insulate, and Seal for Long-Term Performance
Proper flashing, insulation, and sealing are the unsung heroes of any window replacement. Even the best window can leak or draft if water and air find their way around the frame. By following proven techniques for flashing tape application, foam insulation, and precision caulking, you’ll lock out moisture, cut energy loss, and protect your home’s structure for years to come.
Apply Flashing Tape and Waterproof Membrane
Begin by laying a self-adhesive flashing tape along the window sill. Make sure the surface is clean—free of dust, paint blobs, or loose fibers—so the tape bonds fully. Measure the width of the rough opening and cut a length of tape that extends 2 inches past each jamb. Center it on the sill, then press firmly from the middle outward, smoothing out bubbles.
Next, turn your attention to the jambs and head flange:
- Cut vertical strips of flashing tape long enough to run from the sill up past the head flange by at least 2 inches.
- Apply each jamb strip over the edge of the sill tape, working from the bottom up to create a shingle effect that sheds water.
- Finish with a horizontal head flashing, overlapping the jamb tape by at least 2 inches on either side.
This “up-and-over” pattern ensures that gravity carries runoff away from the rough opening. If your product requires a separate waterproof membrane or liquid-applied flashing at the head, apply it now according to the manufacturer’s instructions.
Insulate Gaps with Low-Expanding Foam and Backer Rod
Once the window is shimmed and fastened but before trim goes back on, fill the gap between the frame and rough opening to prevent air infiltration and heat loss. Choose a low- or minimal-expansion spray foam specifically formulated for windows and doors—this will seal voids without bowing the frame.
• Hold the spray tip about 6–8 inches from the gap and inject foam sparingly, watching it expand to fill the space.
• When working with larger gaps (over ½ inch), insert a foam-rubber backer rod first, then seal over it with spray foam. The backer rod saves on foam, provides a consistent backing for caulk, and ensures a uniform joint depth.
Allow the foam to cure—usually 1 to 2 hours—then trim any excess flush with the frame using a utility knife.
Caulk Interior and Exterior Perimeter
Caulking is the final barrier against drafts and moisture. Use an exterior-grade silicone or polyurethane caulk on the outside and a paintable latex caulk indoors for best results.
- Cut the tip of the cartridge at a 45-degree angle to create a 3/8-inch bead.
- Run a continuous bead along the exterior joint between window flange and siding or trim, then smooth it with a wet finger or a caulk tool. Aim for a concave finish that sheds water.
- Inside, apply a neat bead of latex caulk where the frame meets interior trim. Tool it lightly into the joint for a clean, paint-ready surface.
Be careful not to block any weep holes with sealant, and clean up stray caulk with a damp cloth before it skins over. Once everything is dry, reinstall trims and final hardware, confident that your sealing system will stand up to wind, rain, and Colorado’s temperature swings.
Step 10: Install Trim and Complete Finishing Touches
After securing and sealing your new window, trim installation brings the project to life—tying together weather protection and aesthetic polish. Exterior trim and sill adapters not only shed water and shield framing from the elements but also provide a visual capstone to your work. Inside, casings and baseboard molding finish the transition from window to wall, delivering a clean, built-in appearance. Finally, putting hardware back in place restores full functionality. Follow these steps to make sure your new windows look as good as they perform.
Attach Exterior Trim and Sill Adapters
Begin outside by fitting the sill adapter or exterior sill pan. Measure the adapter against the window base and mark weep-hole locations based on the manufacturer’s guidelines—typically two holes near the low points to ensure proper drainage. Use a drill with the specified bit size to create each hole, then hammer the adapter into place, protecting its finish by tapping through a scrap block of wood.
Next, position your exterior trim—whether pre-primed casing or custom-cut boards—so that it overlaps siding or stucco by at least ¼″. Fasten the pieces with corrosion-resistant finish nails, spacing them every 12″ to 16″. Seal the outer edges with a bead of exterior-grade silicone or polyurethane caulk. Smooth the joint with a wet finger or caulk tool to form a tight, water-shedding barrier. Be careful not to block any weep holes; clear drainage is essential for long-term performance.
Install Interior Casing and Baseboard Molding
Inside the room, measure and mark your casing pieces for each side jamb and the head jamb, accounting for any unique angles or reveal widths. Use a miter saw to cut ends precisely at 45°, then dry-fit the pieces to verify alignment. Secure the casing with 1½″ finish nails driven through a nail gun or tapped in with a nail set—avoiding surface dents. Fill each nail indentation with wood filler, let it dry, and sand smooth. Finish with primer and paint or stain to match your décor.
If your window intersects existing baseboard molding, install a thin back band or spacer beneath the casing. This hides any gap and maintains a consistent molding height, giving your window a built-in look that feels intentional and polished.
Final Hardware Reinstallation
With trim in place, bring functionality back by reattaching hardware—locks, crank handles, tilt latches, and decorative grilles—using the screws and brackets you labeled earlier. Slide screens into their tracks, ensuring they sit flush and glide smoothly. Test each operable component: locks should engage firmly, cranks should turn without binding, and sashes should open and close effortlessly. If any hardware feels stiff, apply a small amount of lubricant to hinges and tracks, then retest until everything operates like new.
Now, with trim, caulking, and hardware complete, your windows are fully dressed and ready to handle Colorado’s sun, wind, and snow—performing and looking their best for years to come.
Step 11: Conduct Final Inspection, Cleanup, and Provide Maintenance Tips
After the new windows are snug, sealed, and trimmed, don’t consider the job done until you’ve walked through these final checks and left your home spotless. A thorough inspection, careful cleanup, and clear guidance on upkeep not only protect your investment but also leave you confident in your home’s performance. In this last step, you’ll test every function, clear away the debris, and arm yourself with simple maintenance routines to keep your windows operating like new.
Perform Operational and Quality Checks
Begin inside by cycling each window through its full range of motion. Open and close the sash slowly, listening for any squeaks or sticking points. Locks should engage smoothly, and any tilt‐in or crank mechanisms should feel firm yet effortless. If you notice resistance, minor adjustments to sill shims or a drop of silicone‐based lubricant can restore silky operation.
Next, inspect the seals and weatherstripping. Press gently along the perimeters—there should be no gaps or loose spots. Outside, pour a small stream of water onto the head flashing and sill to confirm proper drainage through the weep holes. Water should flow freely away from the frame, not pool or seep into the opening.
Finally, verify aesthetic quality. Caulk lines should be neat and consistent, nail holes filled and sanded, and paint or stain smooth. Walk each window from multiple angles, both inside and out, to ensure the finish meets your standards. If anything falls short, mark it for touch-up while the crew is still on site.
Clean Up the Worksite and Dispose of Debris
A tidy work area signals a job well done. Start by removing all protective drop cloths and vacuuming dust, glass fragments, and stray shims. Use a stiff-bristled broom for exterior debris, paying special attention to window wells and landscaping beds.
Gather old frames, glass, and trim scraps into heavy-duty contractor bags. Whenever possible, recycle metal and vinyl components—most recycling centers accept clean window scraps. Seal and label any hazardous waste (old glazing compounds or caulking with solvent carriers) and follow local disposal guidelines to keep your project eco-friendly.
As a final touch, wipe down window sills, tracks, and trim with a damp cloth. A quick scout of the surrounding walls and floors ensures no stray marks or scuffs remain. With the cleanup complete, your home will look as though no construction ever took place—save for the beautiful, new windows.
Share Care and Maintenance Guidelines
Maintaining your replacement windows is straightforward, but a little seasonable upkeep goes a long way toward preserving performance and warranty coverage. We recommend the following routine:
- Annual Inspection: In spring or fall, inspect caulk joints, flashing, and weatherstripping. Look for cracks, gaps, or signs of wear.
- Track and Hardware Maintenance: Clean sill tracks and hinge areas to remove dirt buildup. Lubricate moving parts with a silicone spray once a year.
- Re-Caulking: Check interior and exterior caulk beads. Reapply paintable latex caulk indoors and exterior-grade silicone caulk outdoors where sealants show cracking or separation.
- Glass Cleaning: Use a non-ammonia window cleaner and a soft cloth to wash glazing surfaces, preventing abrasive damage to seals.
- Drainage Check: Flush weep holes with a gentle stream of water to clear any debris and ensure proper drainage.
To stay organized, consider a simple maintenance log—whether a printed calendar or a digital spreadsheet. Record inspection dates, any repairs or lubricant applied, and notes on caulk condition. Over time, this log becomes a valuable reference, helping you plan proactive maintenance and extend the life of your investment.
By wrapping up with these final inspections, a systematic cleanup, and clear maintenance steps, you’ll ensure that your new windows deliver comfort, efficiency, and curb appeal for decades to come. Congratulations on completing the window replacement process!
Ready to Upgrade Your Home’s Windows?
By following these steps—from initial planning and precise measuring to professional removal, installation, and finishing—you’ll end up with windows that look great, perform flawlessly, and stand up to Colorado’s temperature swings and storms. Whether you tackle the project yourself or partner with pros, clear goals and careful preparation pay off in comfort, energy savings, and lasting curb appeal.
If a DIY approach feels like too much to handle, our veteran-owned team at Semper Fi Restoration is here to help. We bring Marine-inspired discipline and attention to detail to every job, guiding you through insurance claims, material selection, and expert installation. With our comprehensive window services and follow-up support, you can sit back and watch your home transform—one perfectly sealed window at a time.
Ready to take the next step? Visit our website or give us a call to schedule your free consultation. Let Semper Fi Restoration handle the heavy lifting and turn your window replacement project into a smooth, stress-free experience.
We'd love to do a complimentary roofing assessment for you!
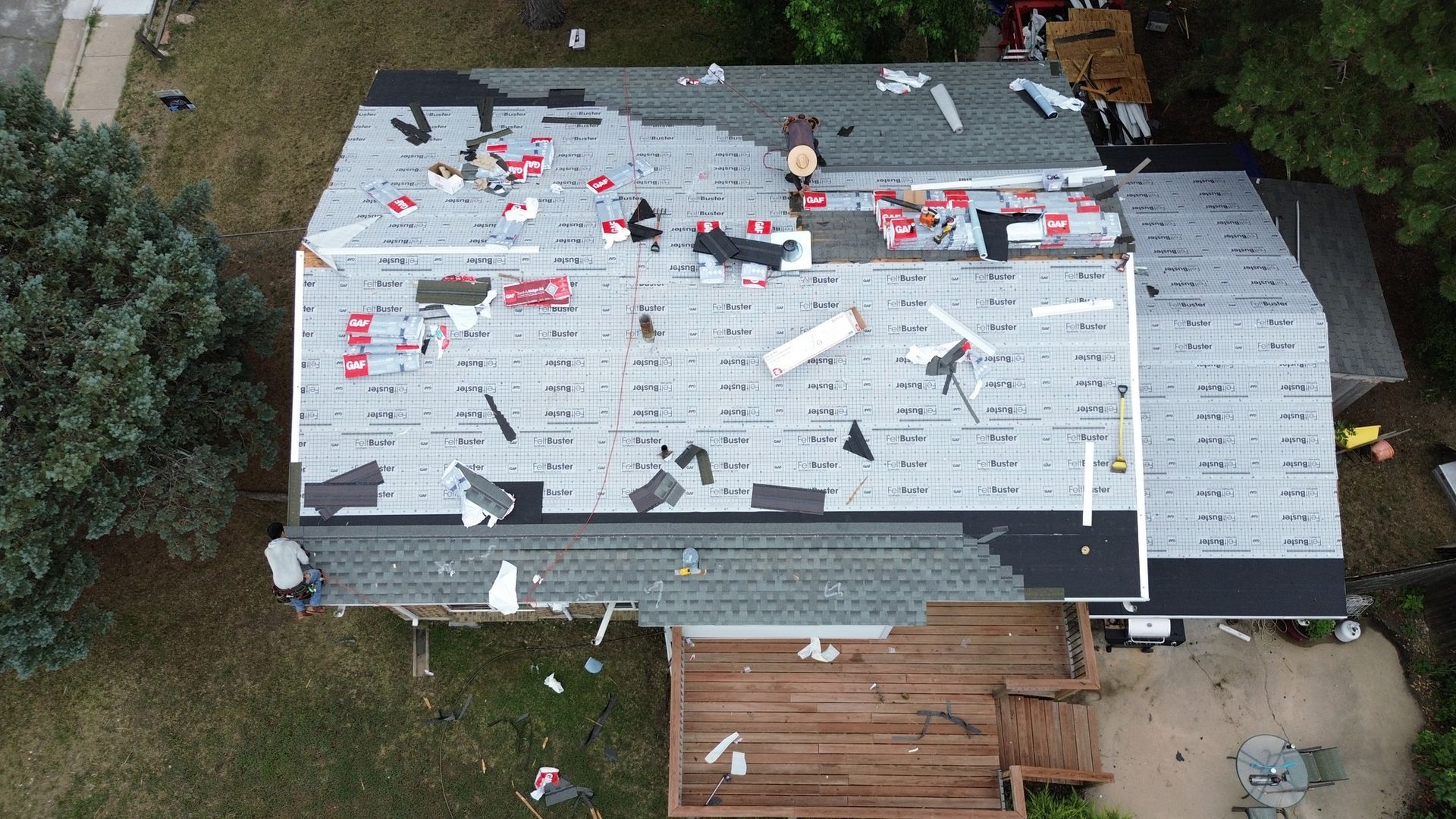