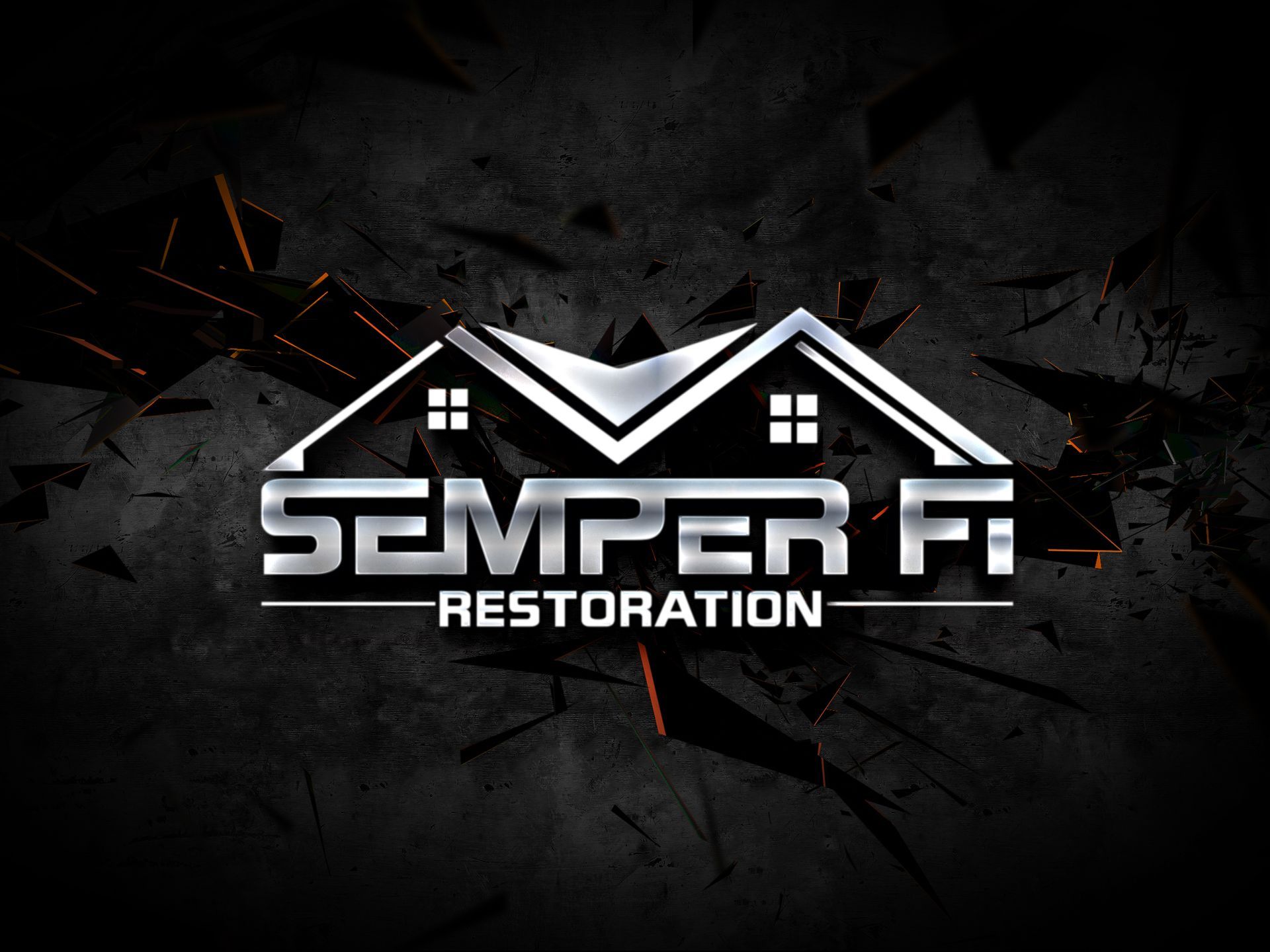
Siding Damage Repair: How To Fix, Patch, And Prevent Issues
A damaged exterior is more than just an eyesore—it’s an open invitation for water, pests, and costly structural headaches. In Colorado, where hail and high winds are routine guests, siding takes the brunt of the assault, whether it’s vinyl, wood, fiber cement, or composite. Even a seemingly small crack or missing section can quickly snowball into rot, mold, or energy loss if left unchecked. For homeowners, knowing how to spot, repair, and prevent siding issues is essential for protecting both curb appeal and the integrity of your home.
This guide walks you through every step of siding damage repair, from the first visual inspection to hands-on fixes for holes, cracks, and failed panels. You’ll learn how to match repair techniques to your specific siding material, which tools and products are worth having on hand, and when it’s time to call in a professional. We’ll cover simple DIY patches, preventative maintenance tips, and expert advice for handling everything from hail dents to long-term moisture threats. Whether you’re facing storm aftermath or routine upkeep, you’ll find the practical, clear steps you need to keep your home’s exterior in top condition—and the peace of mind that comes with it.
1. Inspect and Assess Siding Damage
Before reaching for tools or patch kits, you’ll want to know exactly what you’re dealing with. A careful inspection—both visual and tactile—lets you pinpoint the location, type, and extent of damage so you can choose the right repair strategy. Start by circling your home’s exterior under good lighting, preferably in late morning or early afternoon when shadows highlight surface irregularities. Grab a notepad or your phone to record each issue, and pay special attention to areas beneath eaves, around windows and doors, and where landscaping abuts the walls.
Actionable Inspection Checklist
- Walk your entire perimeter, noting direction (north, south, etc.) and approximate height of damage
- Photograph each defect from multiple angles
- Gently press or tap suspect areas to detect soft spots or hollows
- Lift loose trim or J-channel to check for hidden cracks or moisture
- Look for rusted or missing fasteners and gaps at seams
- Scan for mold, mildew stains, or peeling paint that signal water infiltration
Once all trouble spots are logged, sort them by how serious they appear and identify your siding material (vinyl, wood, fiber cement, composite, or stone veneer). Those two factors—severity and substrate—will guide every step of your repair.
1.1. Identify Visible Damage Types
Siding can fail in many ways. Common examples include:
- Small holes or dents from hail, stray lawn-care debris, or impact
- Hairline cracks that run along a panel or board
- Warping or cupping, often caused by trapped moisture or heat
- Rot or soft spots in wood and composite panels
- Missing sections—whether a single plank or fastener-pop that left a gap
Behind the surface, water intrusion shows up as discolored caulk lines, dark streaks, or mold and mildew growth. If you spot any staining around a seam or trim piece, peel back a corner and feel for dampness. Early detection of moisture is your best defense against structural rot and hidden mold.
1.2. Evaluate Damage Severity
Knowing how bad a problem is helps you decide whether to patch it yourself or call in a pro. We use a simple three-tier scale:
- Minor: Surface blemishes under 1" diameter—small holes, shallow dents, surface cracks.
- Moderate: Damage up to 6" long or cracks extending close to seams—may require a patch or partial panel work.
- Severe: Full-length board/panel failure, widespread warping, major rot, or large missing sections.
Minor damage usually means a quick filler-and-paint job. Moderate issues can be handled with patch kits or section replacements. When you hit the severe category, professional-grade equipment and expertise are safer—and they often come with a warranty on workmanship.
1.3. Determine Your Siding Material
Different siding substrates call for different tools, fillers, and caulks. A quick material ID will keep you from using the wrong patch compound or applying excessive pressure that can crack fragile panels. Here’s an at-a-glance guide:
Material | Key Characteristics |
---|---|
Vinyl | Hollow plastic panels; flex slightly; smooth or wood-grain finish; interlocking edges |
Wood | Visible grain; nail-hole patterns; may have natural warping; accepts wood filler |
Fiber Cement | Very dense, cement-like feel; heavier than wood; chalky when sanded |
Composite | Engineered wood particles; uniform texture; lighter than fiber cement; slight give |
Stone Veneer | Thin stone panels bonded to a backer; mortar joints; heavy and rigid |
Once you’ve mapped out damage and identified your siding type, you’re ready to gather the right tools and materials and move on to the actual repair steps. Up next: safety gear, tool checklists, and prepping your work area.
2. Choose the Right Tools, Materials, and Safety Gear
Before you jump into repairs, make sure you’ve got the right protection, tools, and materials on hand. A little prep goes a long way toward a smooth job—and can keep you from costly mistakes or injuries. Focus on safety first, then stock up on the essentials and consider local rental or purchase options to stay within budget.
2.1. Safety Equipment Checklist
Working on siding often means sharp edges, debris, and heights. Don’t skip these basics:
- Hard hat to guard against falling bits of old siding or loose nails
- Safety glasses or goggles to shield your eyes when prying or sawing
- Work gloves with good grip and cut resistance
- Respirator or dust mask (especially for fiber cement or old paint)
- Hearing protection if you’ll use power saws or drills
- Sturdy ladder or portable scaffolding rated for your height and project weight
Double-check that your ladder is on level ground, and use a spotter if you’re working higher than one story. If you rent scaffolding from a local equipment center, follow the assembly instructions closely and install guardrails for extra security.
2.2. Essential Tools for DIY Siding Repair
A compact toolkit can handle most patch jobs and panel swaps. Start with hand tools, and add power options as needed:
- Pry bar or dedicated siding removal tool for unlocking interlocked panels
- Putty knife (1–2" wide) for applying and smoothing filler
- Sandpaper (100 grit for shaping, 220 grit for final smoothing)
- Utility knife with fresh, sharp blades for clean cuts and caulk removal
- Caulk gun with smooth-trigger action to apron a neat bead of sealant
- Tape measure, chalk line or speed square for precise measurements
Optional power tools speed things up, especially on larger jobs:
- Oscillating multi-tool with sanding and cutting blades
- Cordless drill/driver (with masonry bits for fiber cement)
- Random-orbit sander for textured finishes
2.3. Materials and Patch Kits
Match your materials to the siding substrate and damage type:
- Fillers:
- Exterior-grade wood filler for small gouges or rot on wood boards
- Vinyl patch compound or stick patches for dents and holes in vinyl
- Fiber cement patch kits that include cementitious filler and bonding agents
- Replacement items:
- Full or partial siding panels in your material and profile
- Corner posts, J-channel, and other factory-formed trim pieces
- Sealants and coatings:
- Paintable, exterior-grade caulk with UV resistance
- Primer suited to your siding (e.g., bonding primer for fiber cement)
- Matching exterior paint or paint-and-primer-in-one formulated for your substrate
Most big-box home improvement stores stock these supplies, and many also rent specialty tools if you don’t want to buy. Check local rental centers for ladders or scaffolding, and look for seasonal sales or bulk discounts to lower your overall cost. Once you’re set up, you can move on to prepping the work area with confidence.
3. Prepare the Work Area and Siding Surface
Proper prep is the foundation of any lasting repair. By protecting plants, windows, and hardware—and by thoroughly cleaning the siding—you’ll improve filler adhesion, prevent new damage, and make cleanup a breeze. Aim to work when the forecast is dry, temperatures are between 50°F and 85°F, and humidity is low. That way, caulk, primer, and paint will cure properly.
3.1. Clear and Protect Surrounding Areas
Before you touch the siding, create a buffer zone around your work area:
- Lay down drop cloths or plastic sheeting to catch paint chips, filler, and debris.
- Use painter’s tape to mask off window frames, light fixtures, vents, and any hardware you don’t want to stain.
- Trim back tree limbs or bushes that press against the wall—branches can scratch the siding or scatter debris as you work.
- Move potted plants, patio furniture, and grill equipment out of harm’s way.
Taking these steps up front keeps your yard and home looking neat, and it shortens post-repair cleanup.
3.2. Remove Loose Paint, Caulk, and Debris
A clean, solid surface ensures patch compounds and caulk bond properly:
- Use a stiff putty knife, paint scraper, or even a flat pry bar to peel away flaking paint, old sealant, or weathered caulk.
- Pull rusted or popped-out nails and staples with the claw of a hammer or pliers. Replace any fasteners you remove later with corrosion-resistant nails or screws.
- Knock off dirt, cobwebs, and insect nests with a stiff-bristle brush. Focus on seams, J-channels, and corner posts—any crevice where debris collects.
Removing loose material prevents future peeling, cracking, or water infiltration around your repair.
3.3. Sand, Degloss, and Clean
Once the surface is clear, it’s time to feather and wash:
- Sand the edges of the damaged area with 100-grit sandpaper to remove high spots, then use 220-grit to smooth transitions. For textured or wood-grain siding, gently mimic the pattern with a small sanding block or scraper.
- Mix a mild detergent solution (a few drops of dish soap in a gallon of water) and scrub the repair zone with a soft brush or sponge. This removes oils, mildew, and chalky residue.
- Rinse thoroughly with a garden hose—avoid a pressure washer set above 500 psi, which can drive water behind the siding.
- Allow at least 24 hours for the siding to dry completely before applying filler, caulk, or paint.
A well-prepped, moisture-free surface is the single best way to ensure your siding repair stands the test of time.
4. Repair Small Holes and Dents
Small holes (up to 1" in diameter) and shallow dents are among the easiest siding repairs you can tackle yourself. Filling these blemishes promptly not only restores your home’s good looks but also keeps moisture and pests at bay. A basic filler kit runs around $10–$20, and a pint of matching exterior paint typically costs about $15—making this a budget-friendly weekend project. Follow the steps below for a snug, nearly invisible repair.
4.1. Selecting the Proper Filler
Start by choosing a patch compound that’s formulated for your siding material:
- Wood boards call for an exterior-grade wood filler that expands slightly as it cures to stay flush with the grain.
- Vinyl panels need a vinyl patch compound or a stick patch that flexes with temperature swings.
- Fiber cement siding requires a cementitious filler designed to bond with its dense, concrete-like substrate.
Always check the product label for UV resistance and weather-proofing. A filler that shrinks or chalks out after a few seasons will only send you back to square one.
4.2. Applying the Filler
With your safety gloves on, overfill the void by pressing the compound firmly into the hole or dent using a putty knife:
- Scoop a generous amount of filler onto your blade.
- Force it into the damage, making sure every cavity is filled.
- Scrape off excess compound so the patch stands proud—about 1⁄8" above the surface.
Overfilling ensures that when you sand it back, the repair will settle flush without leaving a gap.
4.3. Smoothing, Sanding, and Texturing
Once the filler is fully cured (check the manufacturer’s cure time, usually a few hours):
- Use 220-grit sandpaper to level the patch until it’s flush with the surrounding siding.
- To mimic wood grain, lightly drag a fine-tooth scraper across the wet filler before it hardens, or press a textured roller into the filler immediately after application.
- For smooth vinyl or composite panels, stick with uniform strokes to blend the patch into the panel’s factory finish.
Take your time here—matching the pattern is what hides the repair from casual view.
4.4. Painting and Blending
A final coat of paint seals the deal:
- If your filler doesn’t include primer, apply a thin layer of exterior primer to the patch.
- Use a paint-and-primer-in-one for vinyl repairs to speed things up.
- Feather brush strokes or dab with a small foam roller, extending paint slightly beyond the patch edges to create a seamless color transition.
Allow the paint to dry fully (usually 2–4 hours) before evaluating if a second light coat is needed. With careful blending and the right materials, your tiny hole or dent will vanish into the background—keeping your siding watertight and looking sharp for seasons to come.
5. Patch Medium to Large Cracks and Splits
Cracks up to 6 inches long or splits running along board seams demand more than a quick dab of filler—but they don’t always require swapping out an entire panel. In this section, we’ll help you decide whether to patch or replace, and walk through using patch kits, trimming patch pieces, and forming a watertight seal.
5.1. When to Patch vs. Replace
Not every crack calls for a full panel swap. Use these guidelines:
• Length of damage: cracks under 6 inches are prime candidates for patching.
• Location: if the split falls entirely within the body of the panel—away from butt joints, corners, or trim—you can usually patch.
• Material type: vinyl and fiber cement both have dedicated patch kits. Wood and composite often require board- or panel-level replacement for structural integrity.
• Movement risk: if the crack crosses an expansion joint or is likely to flex with temperature swings, a replacement may perform better long term.
When in doubt, patch small to moderate splits and plan panel replacement for anything larger than a half-panel or if the damage compromises surrounding fasteners and sealant.
5.2. Using Patch Kits for Vinyl and Fiber Cement
Most big-box and specialty stores stock patch kits designed to match your siding material:
• Vinyl patch kits usually include a premade vinyl patch, adhesive, and touch-up paint or a vinyl-safe filler compound.
• Fiber cement kits come with a cementitious filler, bonding agent, and sometimes a mesh backing to reinforce the repair.
Begin by sanding the crack edges lightly with 100-grit sandpaper to remove loose bits and degloss the surface. Clean the area with a mild detergent solution, rinse gently, and let it dry fully. If you’re working on fiber cement, apply the bonding agent first—this strengthens adhesion and prevents chalking.
5.3. Cutting and Fitting Patch Material
A precise patch hides better and seals more reliably:
- Measure the crack or split, then cut your patch piece so it overlaps the damage by at least 1 inch on all sides.
- For vinyl siding, use tin snips or heavy-duty shears to shape the patch.
- For fiber cement, a fine-tooth carbide-tipped blade on a circular saw or an oscillating multi-tool yields a clean cut.
- Dry-fit the patch, checking that it sits flush with minimal gaps. Trim as needed to follow the panel’s grain or texture lines.
5.4. Sealing Edges and Caulking
Proper edge sealing prevents moisture intrusion:
- Apply a thin bead of exterior-grade, paintable caulk around the entire patch perimeter.
- Use a caulk-smoothing tool or moistened fingertip to tool the bead into a neat, concave fillet.
- Press the patch in place, ensuring caulk squeezes out slightly under the edges—this locks out water.
- Wipe away excess caulk with a damp rag before it skins over.
- Once the caulk cures (per manufacturer instructions), paint the patch and surrounding area to match the rest of your siding.
With the crack filled, reinforced, and sealed, your patch will blend into the panel, keep moisture at bay, and extend the life of your siding until a larger renovation or replacement becomes necessary.
6. Replace Damaged Siding Panels
When cracks, splits, or impact damage go beyond a simple patch—or when you spot a section bowed from hail or a rogue lawnmower nick—you’ll want to replace the entire panel. Swapping panels may sound daunting, but with the right approach you can restore a uniform look, maintain weather resistance, and match your home’s curb appeal. In this section, we’ll cover how to unlock interlocked siding, remove the old boards, prep replacement panels (including color-matching tips), and nail the new pieces in with proper spacing and expansion room.
6.1. Unlocking Interlocked Panels
Start by freeing the panel above the one you’re replacing so you can access the damaged panel’s nailing fin. Slide a siding removal tool—or the rounded end of a putty knife—under the bottom lip of the upper board. Twist gently to disengage the lock, then lift and prop the upper panel with a scrap of wood or have a helper hold it. This exposes the nails on the damaged section without tearing the top board’s locking groove.
6.2. Removing Old Panels and Fasteners
Once the upper panel is secured, use the claw of a hammer or a small pry bar to pull out nails or exterior screws from the damaged panel’s nailing fin. Work from one end to the other, supporting the panel as you go so it doesn’t snap off and damage the house wrap behind it. After removing the board, inspect the house wrap for any rips or punctures. Patch small tears with weather-resistant seam tape, ensuring your moisture barrier stays intact before installing the new panel.
6.3. Measuring, Cutting, and Prepping New Panels
Measure the length of the removed panel between the J-channels or corner posts. Transfer those dimensions to your replacement section and score a straight cut line using a speed square. Cut vinyl with tin snips; use a carbide-tipped blade on wood, composite, or fiber cement. To prevent binding, clip the nailing fin or bottom flange according to the manufacturer’s instructions—this allows the panel to expand and contract without buckling. If the fresh panel color looks too bright against weather-worn siding, apply a coat of exterior primer and matching paint before installation. A paint-and-primer-in-one product can speed up blending and hide that “new board” look.
6.4. Installing and Nailing New Panels
Slip the new panel into the overlap of the board below, then align its nailing fin under the lifted upper panel. Maintain a 1"–1¼" overlap on the panel ends and drive corrosion-resistant nails every 12"–16" along the fin. Position each nail in the center of the elongated slot and leave about 1⁄16" of space between the nail head and the siding—this “proud” nail head gives the panel room to shift laterally as temperatures change. Once fastened, lower the upper panel back into place, locking it securely over the new top edge. Finally, touch up any exposed cut edges or nail heads with matching caulk and paint to seal out moisture and complete a seamless repair.
7. Restore Damaged Corner Posts, J-Channels, and Trim
The finishing touches on your siding—corner posts, J‐channels, window trim, and other profile pieces—do more than look good. They keep moisture out of gaps and direct runoff away from vulnerable edges. Even a small crack in a corner post can let water seep behind the siding, leading to hidden rot or mold. In many cases, you can patch minor blemishes and extend the life of your existing trim. When damage is more extensive, swapping in a new piece ensures a clean, factory‐look joint. Below, we’ll help you decide between patching and replacement, then walk through both processes step by step.
7.1. Assessing Trim Damage
Before grabbing a replacement piece, take a close look at each trim component:
- Cracks and splits: Hairline fractures usually start at bends or where fasteners are set too close to the edge.
- Warped or sagging corners: Heat can soften vinyl profiles, causing them to bow. In wood trim, moisture can lead to cupping or twisting.
- Missing sections or broken return lips: A jostled ladder or hail impact may chip off the narrow flange that locks into the main siding panel.
- Gaps at seams or nail pops: Check if fasteners have pulled through or if caulk has failed—these are early signs a trim piece needs attention.
If damage is limited to a chipped edge or a small crack, you can likely patch it. When you see multiple defects along one piece—especially near interlocking joints or load‐bearing corners—plan on replacement.
7.2. Patching Small Trim Defects
For minor nicks or splits under 6 inches long, a quality exterior filler and paint can work wonders:
- Prep the surface: Lightly sand the damaged area with 100-grit sandpaper to remove loose fragments and degloss the finish. Wipe clean with a damp rag and allow it to dry.
- Apply exterior filler: Choose a flexible, paintable filler designed for your material—vinyl, wood, or composite. Use a putty knife to force the compound into cracks, overfilling slightly.
- Shape and sand: After the recommended cure time, sand with 220-grit paper until the repair sits flush with the surrounding trim. If you’re working on wood, recreate any grain with a fine-tooth tool before the filler fully hardens.
- Prime and paint: Apply a thin coat of primer if the filler requires it, then finish with an exterior paint that matches your trim color. Feather the edges to blend seamlessly.
A well‐executed patch will blend into the profile, keep water out, and buy you another siding season or two without replacing the trim.
7.3. Cutting and Fitting Replacement Trim
When patching won’t cut it—think warped outside corner posts or crushed J-channels—you’ll swap in a new piece:
- Measure accurately: Use a tape measure to capture the full length of the existing trim, including any inside or outside bend. Note the return width (the small lip that holds the siding edge).
- Transfer marks: Lay out the dimensions on the replacement trim piece. For vinyl, use a fine‐tip marker on the back side; for wood or composite, score your cut line with a speed square.
- Cut to size:
- Vinyl and aluminum: snip with tin snips or use a fine‐tooth blade on a miter saw.
- Wood and composite: cut with a miter or circular saw fitted with the appropriate blade.
- Dry‐fit the piece: Slip the new trim into place without fastening. Check that the returns seat firmly into channels on both adjoining siding edges or panels. Minor tweaks with tin snips or a block plane will ensure a snug fit.
With the piece prepped and test-fitted, you’re ready to secure it permanently.
7.4. Securing and Sealing with Caulk
Once your new or patched trim piece is in position, proper fastening and sealing are crucial:
- Fasten with the right hardware:
- Vinyl and aluminum trim: use corrosion-resistant nails or screws, set at least 3⁄8" from the edges.
- Wood and composite: 8d galvanized nails or stainless-steel screws work best.
Drive fasteners into framing or furring strips—not just the siding substrate—to prevent movement.
- Tool a bead of caulk: Apply a continuous bead of paintable, UV-resistant exterior caulk along every seam—where the trim meets siding, at butt joints, and against window or door jambs.
- Smooth for a watertight seal: Run a caulk finishing tool or a wet finger along the bead to form a concave joint that sheds water. Wipe away excess before it skins over.
- Final touch: Once the caulk cures (usually 24–48 hours), touch up nail heads and any exposed cut edges with matching paint.
Following these steps restores the clean lines of your siding envelope, locks out moisture, and keeps your exterior looking sharp season after season.
8. Follow Best Installation Practices to Prevent Future Damage
Even the best repair won’t last if it’s not installed correctly. By following industry-proven techniques for fastening, moisture control, and thermal movement, you’ll make your siding more resistant to hail, wind, and temperature swings. Here’s how to meet—and often exceed—manufacturer and building-code standards.
8.1. Importance of Proper Fastening and Nailing
Correct fasteners are the backbone of a secure siding installation. Too few nails, the wrong type, or improper placement can lead to buckling, blow-offs, or nail pops under wind load.
- Use corrosion-resistant nails or screws rated for your siding material (galvanized steel or stainless steel).
- Fasten into structural members (studs or furring strips), not just the sheathing.
- Align each nail in the center of the factory-punched slot, leaving about 1⁄16" of clearance (a “proud” nail head) so panels can shift laterally with temperature changes.
- Space fasteners every 12–16 inches along each nailing fin to distribute wind load evenly.
- Avoid over-driving: compressed slots restrict panel movement and lead to warping.
8.2. Moisture Barriers and Flashing Best Practices
Moisture management is all about a continuous drainage plane and correct flashing details. If water can’t escape, it will find its way behind the siding and cause hidden damage.
- Install a high-quality house wrap, overlapping seams by at least 6 inches and sealing them with manufacturer-approved tape.
- Cut J-channels and corner trim over the house wrap—don’t slice the barrier—and seal intersections with a thin bead of exterior caulk.
- Flash windows, doors, and other penetrations in a shingle-style sequence (pan below, head flashing above) to redirect water out and away from the wall.
- Fit drip edges or kick-out flashing at roof-to-wall transitions to divert run-off away from siding.
- Ensure window and door sills slope outward at a minimum of 5° for rapid drainage.
8.3. Expansion Gaps and Thermal Movement
Temperature swings cause siding to expand and contract. Without adequate clearance, panels can buckle in summer heat or crack in winter cold.
- Maintain a minimum 1⁄4" gap at panel ends, trim returns, and butt joints when installing in temperatures above 40 °F.
- Increase that gap to 3⁄8" if you’re working below 40 °F—cold materials contract and need extra room.
- Clip nailing fins and bottom flanges per manufacturer guidelines to allow movement within J-channels.
- Avoid binding starter strips or toe-nails—allow the bottom edge to shift vertically as well as side to side.
8.4. Guidelines for Wind and Hail Resistance
In high-wind or hail-prone areas like Northern Colorado, specific standards can greatly reduce damage and insurance headaches.
- Select siding products that meet ASTM D 3679 for impact resistance and UL 2218 for hail rating.
- Follow the fastening patterns and nail-head clearance outlined above for wind uplift protection.
- Reinforce corner posts and trim with impact-rated profiles or metal backers where hail strikes are common.
- For the full installation spec sheet in wind and hail zones, refer to FEMA’s wind and hail guidelines.
- Re-inspect and tighten fasteners after the first major wind event and every two years thereafter to maintain integrity.
By building in these best practices from the start, you’ll avoid the usual pitfalls that lead to failed repairs and premature siding replacement. It’s not just about fixing cracks today—it’s about preventing tomorrow’s headaches.
9. Improve Durability with Moisture Management and Protective Treatments
Effective siding isn’t just about covering your home—it’s about keeping water out long term and choosing materials that stand up to Colorado’s moisture swings. By combining smart design, durable products, and regular upkeep, you can dramatically extend the life of your siding and sidestep decay before it starts.
9.1. Importance of Efficient Moisture Management
Water is siding’s worst enemy, so channel it away before it ever reaches the wall. Start with a consistent drainage plane behind your siding:
- Install a high-quality house wrap or building paper beneath all panels, overlapping seams by at least 6 inches and sealing with manufacturer-approved tape.
- Create a rainscreen gap by using furring strips or a drainage mat—this airspace allows moisture to drain and evaporate, rather than sit against the substrate.
- Incorporate adequate overhangs and drip edges at roof junctions to deflect rainwater away from wall surfaces.
- Grade the soil so that it slopes away from the foundation by at least 4 inches over the first 10 feet, preventing splashback and capillary rise.
These passive design elements work around the clock, ensuring that any moisture on or behind the siding can escape safely.
9.2. Selecting Durable Materials and Preservative Treatments
Not all siding materials weather moisture the same way. Choosing naturally resilient or treated products adds an extra barrier to decay:
- Naturally rot-resistant wood: species like Western red cedar, redwood, and cypress have high tannin content and good dimensional stability.
- Pressure-treated lumber: modern treatments (e.g., ACQ, CA) infuse preservatives deep into the wood, guarding against fungi and insects.
- Protective coatings: borate-based wood preservatives penetrate the substrate to inhibit decay—apply prior to staining or painting for best results.
For more on how wood species and treatments fare against moisture and decay, see the USDA Forest Products Laboratory’s wood durability research. Investing in premium materials up front often saves on repair costs down the road.
9.3. Design Details to Prevent Decay
Small details in your siding installation make a big difference when it comes to water control and ventilation:
- Flashing integration: cut house wrap neatly around windows and doors, then install step-flashing or kerf-mounted flashings in a shingle-style pattern to shed water out and away.
- Vented rainscreens: slot or channel furring strips to create an air gap that promotes drying; combine with insect-screened vent strips at the top and bottom for critter protection.
- Airflow gaps behind siding: maintain a consistent void (typically 1⁄4" to 3⁄8") all around each panel—this prevents moisture locking and encourages continuous airflow.
- Slope for runoff: ensure trim pieces and window sills have a slight downward pitch (minimum 5°) so water doesn’t pool at joints.
By incorporating these measures, you’ll avoid trapped moisture that leads to mold, rot, and fastener corrosion.
9.4. Regular Sealing, Painting, and Inspections
Preventive maintenance keeps moisture seals intact and catches early warning signs before they escalate:
- Annual seal-up: inspect caulk lines around trim, seams, and penetrations every spring, replacing any brittle or cracked sealant with a paintable, exterior-grade caulk.
- Repainting schedule: apply a fresh coat of high-quality exterior paint or stain every 3–5 years (or per manufacturer guidance) to renew waterproof barriers—wood siding may need more frequent resealing in high-UV areas.
- Seasonal check-ups: after heavy winter or hail seasons, walk the exterior looking for chipped paint, loose panels, or dislodged fasteners.
- Professional review: consider a biannual inspection by a siding specialist to assess hidden damage and recommend targeted treatments.
Routine care—coupled with the design and material strategies above—will keep your siding firm, dry, and looking great for decades.
10. Establish a Regular Inspection and Maintenance Routine
Proactive siding care pays off in fewer emergency repairs and lower long-term costs. By committing to a scheduled inspection and maintenance plan—rather than waiting for leaks or rot to appear—you’ll extend the life of your siding, protect your home’s structure, and catch minor issues before they become costly headaches.
10.1. Seasonal Inspection Checklist
Treat each season as its own inspection opportunity. Here’s a quick guide to what you should look for:
Spring
- Examine seams, J-channels, and trim for cracks or failing caulk after winter freeze-thaw cycles.
- Check gutters and downspouts for ice-dam damage or blockages.
- Inspect for loose panels or popped nails where heavy snow may have shifted siding.
Summer
- Look for fading, chalking, or brittle caulk caused by prolonged UV exposure.
- Verify that vents, overhangs, and drip edges are clear of debris.
- Tap a few siding sections to ensure no hollow spots from hidden moisture.
Fall
- Remove leaves and debris from gutters and siding ledges to prevent water pooling.
- Tighten any loose fasteners before winter storms arrive.
- Trim tree branches and vegetation that press against the siding.
Winter
- After heavy snowfall, check for snow or ice accumulation against siding bases.
- Keep an eye out for icicles forming at roof edges—these can damage trim and eaves.
- If interior drafts or cold spots appear, inspect the exterior for compromised siding.
10.2. Cleaning and Washing Methods
Routine washing removes dirt, mold, and pollutants that weaken siding over time:
- Use a garden hose on a low-pressure setting (below 500 psi) and a soft-bristle brush.
- Mix a mild detergent (one ounce of dish soap per gallon of water) to avoid harsh chemicals.
- Rinse thoroughly from top to bottom so that grime flows away from the house.
- Avoid power washers or high-pressure nozzles, which can force water behind panels and damage the moisture barrier.
Aim for an annual cleaning, and spot-wash any stains or mildew as soon as you see them. Keeping the surface free of contaminants will preserve paint, inhibit rot, and prevent stubborn buildup.
10.3. Spot Repairs Before Issues Spread
Small defects are best nipped in the bud. When you spot a cracked caulk line or a hairline panel split, act quickly:
- Reseal worn joints with a high-quality, exterior-grade caulk.
- Fill minor cracks or nail-pop holes with the appropriate patch compound within 30 days of discovery.
- Inspect flashings around windows and doors for gaps, then re-caulk or replace trim as needed.
By addressing these tiny failures promptly, you’ll avoid hidden water intrusion that leads to rot, mold, and more extensive board replacements down the line.
10.4. Budgeting for Ongoing Maintenance and Cost Estimates
Planning a maintenance budget keeps small tasks from becoming big expenses. Here are ballpark figures you can expect:
- Small hole or dent repair: $10–$30 for filler, sandpaper, and paint.
- Trim repair or small patch: $25–$75, including caulk, filler, and primer.
- Partial panel replacement: $75–$200 per panel, depending on material and size.
- Caulking refresh (per linear foot): $1–$3, varies by product and condition.
- Professional maintenance visit: $150–$300 for a basic inspection and minor touch-ups.
Allocate a few hundred dollars per year for DIY supplies, or factor in a professional inspection every 2–3 years if climbing ladders isn’t your thing. A little investment now will save you thousands in premature siding replacement and secondary damage.
11. When DIY Ends: Hiring a Professional Siding Contractor
Sometimes even the best DIYer hits a point where expertise, equipment, or sheer manpower make a pro the smarter choice. Whether you’re staring at widespread hail damage, extensive rot, or simply don’t have the time (or desire) to climb ladders and wrestle with panels, a professional siding contractor can deliver a reliable solution—and usually a warranty to back it up. Here’s how to know when to call in the cavalry, and why Semper Fi Restoration stands out in Northern Colorado.
11.1. Recognizing the Limits of DIY Repairs
Every homeowner has a breaking point. If your project demands working two stories off the ground, cutting dozens of panels, or patching multiple material types, you’re entering pro territory. Safety risks multiply with height and complexity, and an imperfect repair can lead to water infiltration or wind failure down the road. If you’re unsure of your ability to meet manufacturer specifications—like nail spacing, expansion gaps, and moisture barriers—it’s time to hand the job off to trained technicians who live and breathe these details.
11.2. Navigating Insurance Claims and Leveraging Veteran-Owned Expertise
Roof and siding damage from hail or wind often involves insurance claims. A professional contractor not only performs the repair, but can document damage, provide detailed estimates, and liaise directly with your insurer. Semper Fi Restoration’s veteran-led team brings military precision and integrity to every step, ensuring clear communication and honest estimates. Their familiarity with local hail patterns and insurance processes means less guessing for you—and a higher chance of full coverage.
11.3. Semper Fi Restoration’s Siding Repair and Replacement Services
When you’re ready to pass the torch, consider Semper Fi Restoration’s siding repair and replacement services. They handle everything from small patch jobs to complete panel swaps, matching materials and paint to maintain your home’s curb appeal. Their veteran-owned values translate into meticulous prep work, premium materials, and a commitment to getting it right the first time.
11.4. Local Presence in Longmont and Northern Colorado
A contractor who knows your neighborhood is a contractor who can respond quickly. Semper Fi Restoration maintains a strong footprint in Longmont, Brighton, Thornton, and across Greater Denver—check out their dedicated Longmont page to see recent projects and service specifics. Fast turnaround after storms and an on-the-ground crew make post-damage repairs faster and more convenient.
11.5. Comprehensive Exterior Solutions for Your Home
Siding rarely fails in isolation. With Semper Fi’s full suite of exterior services , you can coordinate gutter replacements, siding upgrades, trim repairs, or even exterior painting alongside your siding work. One contractor, one project manager, one seamless timeline—protecting your home from every angle and preserving its value.
Ready to Keep Your Siding in Top Shape
A little attention goes a long way toward preserving the look and performance of your home’s siding. By following regular inspection routines, tackling minor cracks or dents as soon as they appear, and staying on top of seasonal maintenance, you’ll prevent small issues from turning into big headaches down the road. Whether you’re sanding and caulking a hairline split in your fiber cement panels or swapping out a vinyl board after a hailstorm, each proactive step protects your home against moisture, pests, and temperature extremes.
Of course, some jobs call for extra hands—or an expert eye. If you’d rather leave the heavy lifting and precise panel matching to professionals, Semper Fi Restoration is here to help. As a veteran-owned team serving Northern Colorado and the Greater Denver area, we combine military-grade discipline with local know-how to deliver reliable repairs and lasting peace of mind. Ready for a complimentary siding assessment or a full exterior makeover? Visit Semper Fi Restoration to request your free quote and keep your siding—and your home—secure for years to come.
Our Mission
At Semper Fi Restoration, our mission is unwavering:
To defend homes, uphold integrity, and execute every project with the discipline, precision, and relentless commitment that defines us as a veteran-owned, Marine Corps–inspired company.
From Lakewood to Longmont, from Thornton to Sedalia, we serve the communities we call home. These aren’t just job sites—they’re neighborhoods where we’ve shaken hands, climbed ladders, earned trust, and protected families.
We don’t just repair roofs—we defend homes and safeguard peace of mind.
In a region where hail, wind, and unpredictable weather strike hard, we hold the line where it matters most—your rooftop. In an industry full of shortcuts and quick-fix promises, we remain grounded in principles: discipline, precision, and purpose.
Our crews operate with the rigor of a military unit—organized, reliable, and mission-focused. We are selective in who we bring onto our team, because every person represents our name, and every nail we drive carries our reputation.
We don’t cut corners. We don’t accept mediocrity.
Accountability is our foundation. We demand it from ourselves and deliver it to our clients. From Commerce City to Erie, every inspection, every estimate, and every completed job is a reflection of the standards we refuse to lower.
Every project is a mission. And we don’t miss.
We approach each roof with clear communication, disciplined planning, and an unshakable commitment to excellence. Because when we say we’ll protect your home, we mean it—every task, every detail, every time.
Built to endure. Driven by pride. Rooted in Colorado. Led by purpose.