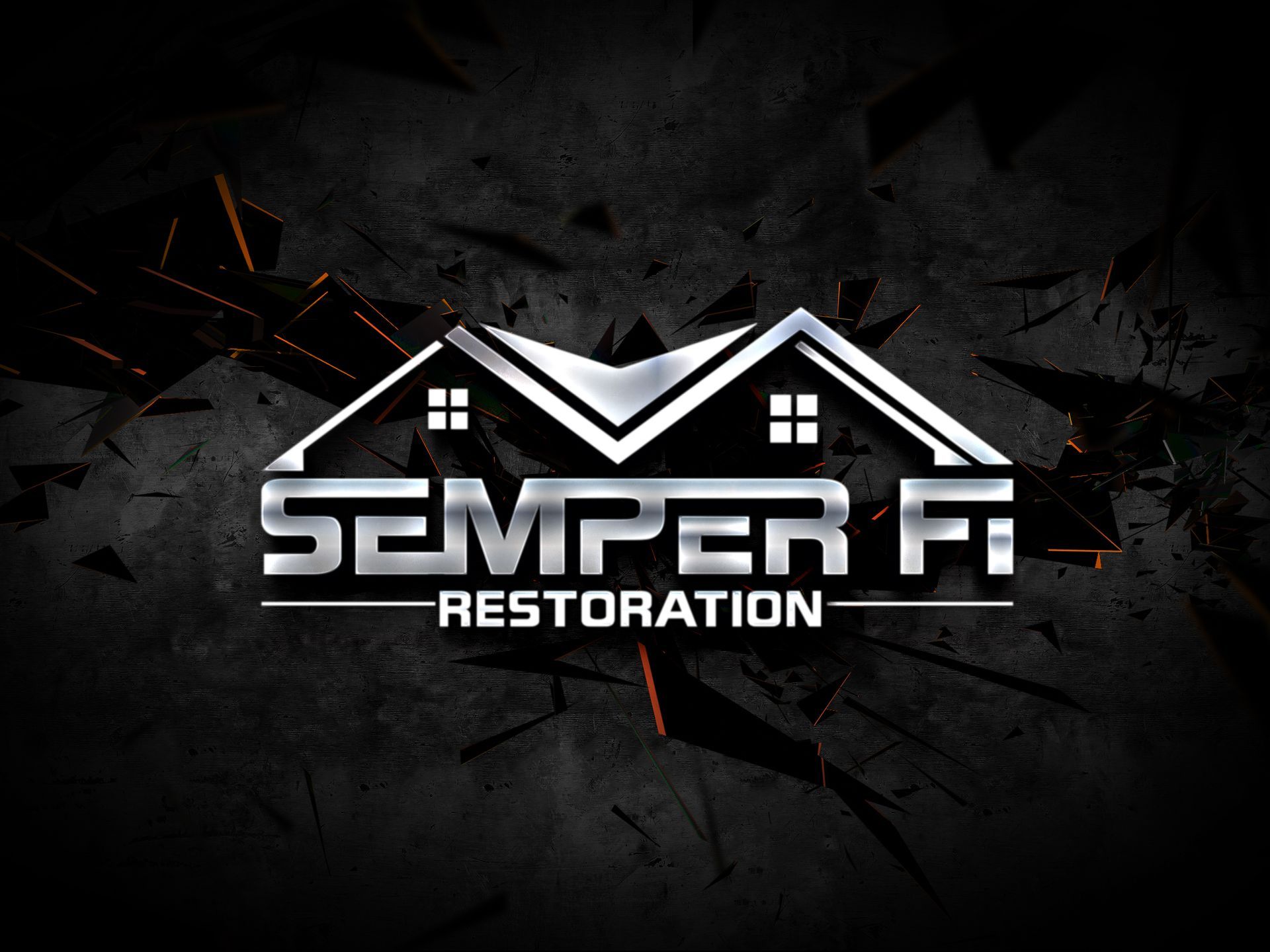
Window Repair vs Replacement: How to Choose the Best Option
A chilly draft sneaking through the living room, a stubborn window that won’t budge, or a telltale water stain after a Colorado hailstorm—these are the kinds of issues that put your home’s windows front and center. Windows do more than frame a scenic view; they quietly shape your comfort, energy bills, and even your home’s security and value. Yet when damage or age catches up, homeowners face a pivotal decision: is it smarter to repair that window, or is full replacement the way to go?
The answer isn’t always obvious, and making the right call can mean the difference between a simple, cost-effective fix and a wise investment that pays off for years. With so much at stake—from curb appeal to utility costs and resale value—it’s worth taking a strategic approach before picking up the phone or reaching for a toolbelt.
This guide breaks down the repair-versus-replacement dilemma step by step, empowering you to spot the signs, weigh your options, and plan your next move with confidence. Whether you’re dealing with post-storm damage in Thornton, drafty old frames in Longmont, or just want to boost your home’s efficiency, you’ll find a clear 10-step process to help you choose the best path forward.
Step 1: Evaluate Your Window’s Current Condition
Before diving into repairs or calling in pros, take a methodical look at each window. A thorough assessment not only pinpoints the real issues but also prevents unnecessary work and surprise costs down the line. Set yourself up for success by gearing up: slip on durable gloves, pop on safety glasses, and make sure any ladder you use is firmly planted on level ground. With safety covered, you can move on to a clear, step-by-step inspection.
Inspect Glass for Cracks, Chips, and Fogging
Start with the glass itself. Run your eye along every pane, looking for hairline cracks or chips that could spread under stress. Pay close attention to corners and edges—these are where small fractures often begin. Next, check for moisture. If you see mist or droplets on the outside surfaces after a humid day, it’s usually harmless condensation. But if fog appears sandwiched between two panes of an insulated glass unit (IGU), that seal has failed. In most cases, fogged IGUs need full replacement to restore clarity and insulating performance.
Examine Frame and Surrounding Woodwork
Shut the window and examine the frame and sash cavities. Use a flat-head screwdriver or awl to gently probe wood in hidden corners—if the tool sinks in without resistance, you’ve likely found rot. Look for visual clues too: water stains, blistered or peeling paint, and warped or swollen wood all signal past or ongoing moisture intrusion. Don’t forget exterior trim, drip caps, and sill details; damage here can let rain sneak in behind what looks like a solid frame face.
Test Operation: Opening, Closing, and Locking
Finally, put the window through its paces. Slide each sash up and down, then latch and unlock it as you would daily. Smooth motion is the goal. If you feel catching or grinding, common culprits include:
- Excess paint build-up between sash and jamb
- Tracks out of alignment or clogged with dirt
- Hinges, pulleys, or balances that have corroded or worn out
Often, a little cleaning, lubrication, or a quick hardware swap will get things moving again. By noting which components stick or strain, you’ll know whether a simple tune-up will do or if it’s time to explore deeper repairs or replacement.
Step 2: Identify Repairable Window Issues
Not every window woe calls for a full replacement. In fact, many issues—especially those that affect appearance or basic operation—can be fixed quickly and affordably. Tackling these repairable problems keeps your windows functional, extends their lifespan, and avoids the higher price tag of new installations. Below are the most common repair categories and how to handle them.
Cosmetic Repairs: Paint, Casing, and Caulking
Peeling paint, cracked or loose casing, and failing caulk don’t just look rough—they let moisture and drafts sneak in. Start by scraping away old, flaking paint and sanding the surface smooth. When old caulk has split or pulled away from the frame:
- Use a utility knife or caulk-removal tool to clear out gaps.
- Load an exterior-grade caulking gun with a paintable silicone or polyurethane sealant.
- Apply a continuous bead along the joint, then tool it smooth with a damp finger or caulk tool.
After the sealant cures, prime bare wood with a weather-resistant primer and finish with two coats of high-quality exterior paint. These steps restore your window’s curb appeal and prevent future water damage—all for under $50 per window in materials, plus minimal labor if you DIY.
Hardware and Functional Repairs
Sticking sashes, broken locks, or a pulley that won’t hold weight can usually be fixed without swapping out the entire window. A basic tune-up involves:
- Cleaning tracks: vacuum debris, then wipe with warm, soapy water.
- Lubricating moving parts: spray a silicone-based lubricant into hinges, balances, and pulleys.
- Replacing worn pieces: upgrade sash balances, tilt latches, locks, or crank handles as needed.
Most homeowners find that a professional service call for these fixes runs from $150 to $400, depending on how many windows and parts are involved. Tackling hardware repairs not only restores smooth operation but also improves security and energy performance.
Glass Seal and Weatherstripping Maintenance
Seals between panes can deteriorate over time, and weatherstripping often compacts or shreds—both of which let air and moisture inside. To refresh these seals:
- Swap out old weatherstripping: foam tape, V-seal, or bulb gaskets are easy to cut to length and press into the frame.
- Reseal minor gaps between glass and frame: apply a glazing compound designed for exterior use, then smooth it with a putty knife.
Regularly inspecting and replacing weatherstripping (every 3–5 years) keeps your windows airtight and significantly reduces drafts. A few rolls of quality weatherstripping cost under $20 per window, making this one of the most budget-friendly repairs you can do.
By focusing on these repairable issues, you’ll often restore function and appearance at a fraction of the cost—and delay or even avoid the need for full window replacement.
Step 3: Determine When Replacement Is the Better Choice
Even the most diligent repair efforts won’t save every window. Some issues go beyond a quick patch or hardware swap and mean it’s time for a full replacement. Recognizing these tipping-point problems early helps you avoid wasted repair dollars and keeps your home safe, secure, and energy efficient.
Broken or Missing Glass Panes
A cracked or shattered pane isn’t just an eyesore—it’s a safety hazard. Broken glass exposes your home to the elements, compromises security, and can injure family members or pets. Single‐pane windows are especially risky, since any impact can send shards flying inward. Multi-pane units fare better, but lost or damaged seals during glass‐only repairs often mean the entire insulated glass unit (IGU) must be replaced to restore both clarity and thermal performance. When a pane is missing or irreparably cracked, full window replacement is usually the faster, more cost‐effective solution than trying to source and reseal individual glass sheets.
Severe Frame or Structural Damage
Minor rot or paint peeling can be sanded and sealed, but when the frame itself is compromised, repairs become a temporary fix at best. Extensive wood rot, warping, or a bowed sash indicates long-term moisture intrusion and potential mold growth inside the wall cavity. Even if you patch over the worst spots, underlying deterioration will continue, often at accelerated rates. Structural integrity matters not just for weather protection but also for the window’s ability to carry loads and stay anchored in its opening. When probe tests reveal widespread “soft” spots or you notice gaps that can’t be caulked shut, it’s safer to invest in replacement windows with new frames built to today’s moisture-resistant standards.
Chronic Drafts and Energy Inefficiency
You’ve tried repainting, recaulking, and swapping weatherstripping, yet cold spots and drafty breezes remain. That’s a clear sign the window’s thermal envelope has failed—either through single‐pane glass, a broken seal in a multi-pane unit, or an aging frame that no longer insulates. Drafts aren’t just uncomfortable; they force your HVAC system to work overtime, hiking up utility bills. Industry data shows replacement windows run anywhere from $300 to $2,500 per opening, with an average installed cost of about $750. But when energy savings and improved comfort are factored in—plus potential rebates for ENERGY STAR®-rated models—the upfront investment often pays for itself over time. If you see persistent cold spots or your heating and cooling costs keep climbing despite repairs, replacement is likely the best path forward.
Step 4: Compare Costs and Long-Term Value
Any window decision comes down to dollars and sense—comparing what you spend today with what you’ll save (and recoup) tomorrow. In this step, we’ll break down typical repair and replacement costs, then look at how new windows can boost your home’s value and pay for themselves over time.
Repair Cost Breakdown
Repairs are often the most budget-friendly path, but it helps to know the ranges you’re likely to see:
- Reglazing broken seals or minor glass chips: $100–$200 per pane
- Hardware replacement (locks, balances, handles): $75–$150 per window
- Weatherstripping refresh: $20–$50 in materials
- Full repaint and recaulk: under $300 per window, including primer, paint, and sealant
For example, if you spot peeling paint and failing caulk, a combo repaint-and-reseal job might run you $250. Tack on a sash balance swap for $120, and you’ve still spent under $400 to restore appearance, security, and draft protection—often extending your window’s life by several years.
Replacement Cost Breakdown
When a repair won’t cut it, replacement windows come with a wider cost spectrum:
- Budget vinyl single- or double-pane: $300–$600 installed
- Mid-range wood or fiberglass frames with double-pane glass: $600–$1,200
- Premium styles (triple-pane, custom shapes, specialty coatings): $1,200–$2,500+
Across Northern Colorado, the installed average hovers around $750 per window. Factors that drive price include frame material, glass type (double vs. triple pane), hardware grade, and any custom dimensions or grid patterns.
Return on Investment and Home Value
A new window isn’t just an expense—it’s an investment. According to industry data, most homeowners recoup 70–80% of replacement window costs at resale. On top of that, energy-efficient models can shave hundreds off annual utility bills. Here’s a quick look at payback math:
Payback Period = Cost / Annual Savings
Installed Window Cost | Estimated Annual Energy Savings | Payback Period |
---|---|---|
$750 | $150 | 750 / 150 ≈ 5 years
|
$1,200 | $180 | 1200 / 180 ≈ 6.7 years
|
Even in a climate with intense sun and cold snaps, trimming your heating and cooling bill by $100–$200 per year adds up. Over a decade, that’s $1,000–$2,000 saved—on top of the home-value boost when you decide to sell.
By stacking repair costs against replacement figures and factoring in energy and resale returns, you’ll see exactly where your money does the most work. In the next section, we’ll look at energy performance ratings to fine-tune your choice even further.
Step 5: Factor in Energy Performance Ratings
Choosing the right windows isn’t just about looks—it’s about understanding how they perform against heat, cold, and sun. Energy performance ratings give you the numbers to compare options objectively and select units that will keep your home comfortable while lowering utility bills. Here’s how to read those labels, why ENERGY STAR® matters, and how to run the numbers on potential savings.
Understanding NFRC Labels
All reputable windows display a National Fenestration Rating Council (NFRC) label, which you can explore on the U.S. Department of Energy’s energy performance ratings page. Key metrics include:
- U-factor: Measures heat transfer rate; lower values mean better insulation.
- Solar Heat Gain Coefficient (SHGC): The fraction of solar radiation admitted; lower SHGC limits overheating in summer.
- Air Leakage (AL): Indicates how much air seeps through; tighter windows have lower AL.
- Visible Transmittance (VT): The amount of natural light transmitted; higher VT means brighter indoor spaces.
- Condensation Resistance (CR): Scores a window’s ability to resist moisture build-up; higher CR reduces fogging.
For Colorado’s mix of hot summers and cold winters, aim for:
Metric | Recommended Range | Benefit |
---|---|---|
U-factor | ≤ 0.30 | Cuts winter heat loss |
SHGC | 0.25 – 0.40 | Balances solar gain and shade |
Air Leakage (AL) | ≤ 0.30 cfm/ft² | Minimizes drafts |
Visible Trans. | ≥ 0.40 | Maximizes daylight |
Condensation (CR) | ≥ 45 | Reduces moisture on glass |
The Benefits of ENERGY STAR® Certified Windows
ENERGY STAR® uses NFRC data plus regional climate zones to identify top performers. In Colorado’s Northern region, ENERGY STAR certified windows must meet stricter U-factor and SHGC thresholds—so you know they’ll deliver real-world comfort and savings. Beyond lower heating and cooling costs, you’ll enjoy:
- More consistent indoor temperatures with fewer hot or cold spots.
- UV protection that helps prevent fading on carpets and furnishings.
- Reduced drafts for quieter, cozier rooms.
Calculating Energy Savings
To see the impact of a lower U-factor, try a simple back-of-the-envelope calculation. Use this formula:
Annual Energy Savings (kWh) = ΔU-factor × Window Area (ft²) × HDD × 24 / 3412
Where:
- ΔU-factor is the difference between old and new U-values
- HDD is annual heating degree days (around 5,000 for Denver)
- 3412 converts BTUs to kWh
For example, upgrading 200 ft² of old windows from U 0.30 to U 0.20:
= (0.30 – 0.20) × 200 ft² × 5,000 × 24 / 3412 ≈ 70 kWh/year
At an average rate of $0.12/kWh, that’s about $8 per window per year. Scale that across your home, and the savings add up quickly.
For a more precise picture, leverage online energy savings calculators or schedule a professional energy audit. Armed with exact figures, you can make a confident decision that balances cost with comfort and long-term value.
Step 6: Explore Rebate and Tax Incentive Opportunities
Upgrading or replacing windows can be a sizable investment, but you don’t have to cover the full cost on your own. Federal tax credits, state rebates, and utility incentives can reduce your out-of-pocket expense and speed up your payback. In this step, we’ll show you where to find these programs, how to qualify, and what documentation you’ll need to collect.
Use DSIRE to Find Available Programs
The DSIRE database is the most comprehensive source for federal, state, and local clean-energy incentives. To get started:
- Go to the DSIRE site and enter your ZIP code.
- Filter by “Residential” and then by “Windows/Doors/Skylights” or “Insulation.”
- Review eligibility criteria, application deadlines, and incentive amounts.
Each program listing includes contact information for administrators—often state energy offices or local utilities—so you can call or email for detailed guidance. Bookmark your results and note any required pre-approval steps, such as ordering ENERGY STAR® products before installation.
Federal Tax Credits for ENERGY STAR® Windows
Homeowners installing qualifying ENERGY STAR® windows may be eligible for the Energy Efficient Home Improvement Tax Credit, which covers:
- 30% of the total cost (materials plus labor)
- Up to $600 per year, through December 31, 2032
To claim the credit:
- Purchase windows that carry the ENERGY STAR® label and have NFRC ratings.
- Retain manufacturer’s certification statements, receipts, and proof of installation dates.
- Complete IRS Form 5695 when you file your annual return.
Keep a digital folder or physical binder with all documentation. If the program rules change, your organized records will simplify any audit or adjustment requests.
Colorado-Specific Rebates and Utility Incentives
Colorado homeowners have additional opportunities to save. The Colorado Energy Office periodically rolls out rebate programs for energy-efficient upgrades—watch their website or sign up for bulletins to catch new windows incentives. Beyond the state level, many Northern Colorado utilities offer rebates on qualified window projects:
- Xcel Energy’s Home Energy Rebate program
- Black Hills Energy residential efficiency incentives
- Local co-ops like Poudre Valley REA and Holy Cross Energy discounts
Each utility sets its own rebate amount—sometimes up to $100 per window—so check your provider’s online portal or give them a quick call. If you work with a contractor, they can often handle the rebate paperwork on your behalf, ensuring you don’t miss deadlines or documentation requirements.
By tapping into DSIRE, federal tax credits, and Colorado-specific programs, you can slash hundreds—or even thousands—off the cost of your window upgrade. In the next step, we’ll help you decide whether to tackle repair tasks yourself or bring in the pros.
Step 7: Decide Between DIY Repair and Hiring a Professional
At this point, you’ve evaluated your windows, weighed repair versus replacement, and even looked at rebates and energy ratings. Now comes a practical question: should you roll up your sleeves and tackle the work yourself, or bring in a qualified contractor? Your decision will hinge on your comfort level, the complexity of the project, and the stakes involved—from safety and warranties to potential insurance claims after a hailstorm or wind event.
Pros and Cons of DIY Window Repair
DIY window repair can be tempting—especially when you factor in the savings on labor. On the plus side, a motivated homeowner can:
- Save on service call fees and labor (often 40–60% of the total cost)
- Control scheduling and work at your own pace
- Learn new skills and maintain a sense of accomplishment
On the flip side, the DIY route carries some risks:
- Mistakes can lead to leaks, drafts, or damaged frames—costing more down the road
- Lack of a warranty means any follow-up fixes come out of your pocket
- Safety concerns, particularly when working at heights or handling broken glass
- Time investment can eat into weekends or evenings
If you feel confident using basic tools—utility knife, caulk gun, screwdrivers—and you’re only refreshing caulk, replacing weatherstripping, or swapping a broken lock, DIY might make sense. But when projects grow in size or complexity, it’s time to think about professional help.
When to Call in the Experts
There are clear signs that a seasoned window technician is the better choice:
- Major structural repairs: Extensive rot, warped frames, or compromised jambs require precise carpentry and moisture-resistant materials.
- Glass replacement in IGUs: Pulling apart multi-pane units and resealing them demands factory-grade equipment and airtight seals.
- Post-storm damage and insurance claims: After hail or high-wind events, professional inspection ensures accurate damage reports, documentation, and an insurance-approved scope of work.
- Custom or large-scale projects: Picture windows, bay units, and specialty shapes often come with longer lead times and technical installation requirements.
A professional brings insured workmanship, manufacturer warranties, and the peace of mind that repairs or replacements meet local building codes.
How to Prepare for a Professional Visit
Getting the most out of your contractor’s time helps the project move smoothly and keeps costs predictable. Before the installer arrives:
- Clear the immediate work area: move furniture, planters, and décor away from each window.
- Secure or relocate pets to reduce stress and keep walkways open.
- Wipe down sills and remove any curtains or blinds to give unobstructed access.
- Photograph existing damage and list any concerns or questions so you can review them on-site.
- Confirm access points—garage, side doors, ladders—and any parking or permit requirements.
By doing a little prep up front, you’ll help the team focus on repairs or installations rather than logistics. The result? Cleaner workspaces, faster completion, and a clear understanding of the final deliverables and warranty coverage.
Step 8: Select the Best Window Service Provider
With your project scope defined—from minor repairs to full replacements—the next critical step is finding a partner you can trust. The right contractor will bring technical expertise, clear communication, and solid warranties, ensuring your investment pays off in durability and performance. As you evaluate options, focus on three key areas: specialized local providers, credentials and customer feedback, and detailed bids that let you compare apples to apples.
Semper Fi Restoration: A Veteran-Owned Local Choice
Semper Fi Restoration stands out for homeowners across Northern Colorado and the Denver metro. Veteran-owned and operated, the company combines Marine Corps values of integrity and precision with deep knowledge of Colorado’s weather challenges. Whether you need impact-resistant units after hail damage or want to upgrade to ENERGY STAR® windows, Semper Fi offers tailored solutions:
- Energy-Efficient Custom Windows: Explore high-performance options built for Colorado’s climate at https://semperfirestoration.com/window-solutions
- Local Longmont Window Installations: Benefit from fast response times and neighborhood expertise at https://semperfirestoration.com/semper-fi-restoration-longmont
- Integrated Exterior Restoration: Bundle your window work with roofing, siding, and gutters for a seamless exterior project at https://semperfirestoration.com/roof-repair-services-free-quotes-expert-local-pros
Choosing a contractor with local roots means they understand permit processes, HOA guidelines, and typical rebate opportunities. Plus, their branded trucks and veteran-led team reinforce trust at every step.
Checking Credentials, Reviews, and Warranties
Before you sign on the dotted line, verify each contender’s qualifications:
- Licensing & Insurance: Confirm they hold a Colorado contractor’s license and carry liability and workers’ compensation coverage.
- NFRC Certification: Ensure installers are familiar with NFRC performance standards so your new windows meet the promised U-factors and SHGC ratings.
- Online Feedback: Read recent reviews on Google, Yelp, and the Better Business Bureau—look for consistency in praise (and any recurring red flags).
- Warranty Coverage: Ask about both manufacturer warranties on the windows themselves and labor guarantees from the installer. A solid labor warranty often spans 5–10 years, covering seal failures, hardware malfunctions, and installation issues.
A contractor who openly shares credentials, points you to verifiable reviews, and backs their work with clear warranties is likely to deliver a smooth, reliable project.
Getting and Comparing Multiple Bids
Don’t settle for the first estimate—request detailed quotes from at least three qualified providers. A comprehensive bid should break out:
Item | Provider A | Provider B | Provider C |
---|---|---|---|
Window model & specs | |||
Frame material | |||
Glass type & coatings | |||
Labor & install fees | |||
Warranty (materials) | |||
Warranty (labor) | |||
Total cost |
Comparing line by line helps you spot hidden markups, assess the relative value of higher-end materials, and make a fully informed choice. Once you’ve weighed expertise, pricing transparency, and after-sale support, you’ll be ready to select the partner that best aligns with your budget, timeline, and quality expectations.
Step 9: Plan and Schedule Your Window Project
With a contractor selected and your scope defined, it’s time to map out the logistics. A well-crafted plan keeps surprises at bay, minimizes downtime, and ensures your home stays protected throughout the process. In this step, we’ll cover how to build a realistic schedule, prepare your living spaces, and know exactly what to expect on installation day.
Creating a Realistic Timeline
Every window project follows a similar rhythm, but details can shift based on custom orders and local demand. Here’s a common four-week outline:
- Week 1: Assessment & Final Specs
Your installer performs a detailed measurement and confirms any custom features—grids, triple-pane glass, or specialty coatings. - Weeks 2–3: Manufacturing & Delivery
Custom windows often take two to three weeks in factory production, especially during spring and summer when demand peaks. - Week 4: Installation
Crews arrive to remove old units, prep openings, and fit new windows. A typical day covers two to four standard-sized frames, depending on crew size. - Week 5: Inspection & Touch-Up
After the dust settles, you’ll walk through each opening with the contractor, verify seal quality, and address any final caulking or paint touch-ups.
Adjust this template if you’re working with off-the-shelf units, historic restorations, or HOA review periods. Your contractor should give you a firm start date once windows are on the way and manpower is locked in.
Preparing Your Home for Installation
Good prep saves time and protects your belongings. Consider these housekeeping and permit tips:
- Clear the Workspace
Move furniture, plants, and décor at least three feet from each window. Cover flooring or shrubs with tarps if installers will be framing from the inside or outside. - Secure Pets and Kids
Let the team know if any areas are off-limits, and plan to keep pets in a separate room—both for their safety and to avoid accidental escapes. - Check Permits and HOA Rules
If your community requires approval for exterior changes, submit applications 2–4 weeks in advance. Your contractor can often handle permits on your behalf. - Confirm Access Points
Ensure a clear path from driveway to work area. If you have side gates or limited off-street parking, communicate these details early so the crew can plan equipment staging.
A few hours of prep on your part can translate into a faster install and a cleaner finish.
What to Expect on Installation Day
The big day can feel busy, but knowing the routine will help you stay relaxed:
- Arrival and Walk-Through
Installers arrive with tools, windows, and protective gear. They’ll review the plan and safety measures, then mark any final reference points. - Old Window Removal
Panels come out first, followed by trim and any rotten framing. Expect some dust and minor debris—contractors should keep drop cloths ready. - Installation and Sealing
New frames go in, shims are adjusted for level and plumb, and the crew insulates gaps with low-expansion foam. Interior and exterior caulking follow. - Clean-Up
Most reputable teams vacuum debris and remove drop cloths before packing up. A final wipe-down of sills and hardware ensures you’re left with nothing but sparkling new glass. - Final Walk-Through and Sign-Off
You’ll inspect each window—testing operation, checking seals, and noting any touch-up needs. Once everything meets your satisfaction, you sign off on completion and warranty paperwork.
By the end of the day, you’ll have a clear understanding of care instructions, warranty coverage, and the contractor’s contact info for any future questions. With your home freshly outfitted, all that’s left is to sit back and enjoy the view.
Step 10: Maintain Your Windows for Long-Lasting Performance
Even the best windows need a little TLC to stay in top shape. Regular care helps prevent minor wear from turning into major headaches and keeps your home comfortable, safe, and energy-efficient for years to come. By carving out a few minutes each season and keeping an eye on small issues, you’ll protect your investment and extend the service life of every opening.
Routine Cleaning and Inspection Practices
Start with a quarterly checkup. At least four times a year, wipe down glass and frames with a mild, non-abrasive cleaner and a soft cloth. Rinse off any residue so dirt and grit don’t scratch the surface. Stroke your fingers along weatherstripping and caulk lines to feel for cracks or separations. Spin or slide hardware—hinges, rollers, locks—and if you notice friction, spray a silicone-based lubricant. Jot down anything that looks worn: a tiny blister in the wood, a fibrous gap in a seal, or a loose screw in the sash. Catching these early means you can tighten, re-seal, or replace a part before it makes a bigger mess.
Seasonal Maintenance Checklist
Different times of year bring different demands. A quick seasonal to-do list could look like this:
- Spring: Inspect exterior caulk and repaint any peeling spots; clear debris from tracks and screens.
- Summer: Lubricate all moving parts; wash glass to maximize daylight; check condensation resistance after humid spells.
- Fall: Trim back bushes and branches that brush against windows; reseal glass-to-frame gaps before winter chills.
- Winter: Scan for drafts around sills and weatherstripping; top off any failed caulk beads to keep cold air out.
Adjust this calendar based on your local micro-climate—Colorado sun and snow can age seals faster than a gentler setting. A few well-timed maintenance tasks will keep your windows in prime condition through hail, wind, and freeze-thaw cycles.
Addressing Minor Issues Early
Tiny problems left alone have a knack for ballooning into big repairs. If you spot a hairline crack in the glazing compound, re-tool it with fresh glazing before moisture seeps in. Loose handles or wobbly lock strikes can often be tightened on the spot; if hardware has reached end of life, swapping in a new balance or latch usually takes under an hour. By nipping drips, gaps, and squeaks in the bud, you’ll avoid costly replacements and preserve smooth operation. A stitch in time really does save nine—and in this case, it might save you hundreds in labor and materials down the road.
Moving Forward with Your Window Upgrade
You’ve now walked through a clear, 10-step roadmap—from diagnosing damage and weighing repair versus replacement to understanding energy ratings, incentives, and professional partners. By following this process, you’ll make a decision that fits your budget, boosts home comfort, and maximizes long-term value. A thoughtful approach today means fewer drafts, lower utility bills, and windows that perform beautifully for years to come.
When you’re ready to turn your plan into reality, trust the veteran-owned team at Semper Fi Restoration. We offer complimentary window assessments, expert installations, and seamless coordination with insurance claims or rebates—so you can move forward confidently. Visit our homepage to schedule your free consultation and take the next step toward brighter, more efficient windows.
Our Mission
At Semper Fi Restoration, our mission is unwavering:
To defend homes, uphold integrity, and execute every project with the discipline, precision, and relentless commitment that defines us as a veteran-owned, Marine Corps–inspired company.
From Lakewood to Longmont, from Thornton to Sedalia, we serve the communities we call home. These aren’t just job sites—they’re neighborhoods where we’ve shaken hands, climbed ladders, earned trust, and protected families.
We don’t just repair roofs—we defend homes and safeguard peace of mind.
In a region where hail, wind, and unpredictable weather strike hard, we hold the line where it matters most—your rooftop. In an industry full of shortcuts and quick-fix promises, we remain grounded in principles: discipline, precision, and purpose.
Our crews operate with the rigor of a military unit—organized, reliable, and mission-focused. We are selective in who we bring onto our team, because every person represents our name, and every nail we drive carries our reputation.
We don’t cut corners. We don’t accept mediocrity.
Accountability is our foundation. We demand it from ourselves and deliver it to our clients. From Commerce City to Erie, every inspection, every estimate, and every completed job is a reflection of the standards we refuse to lower.
Every project is a mission. And we don’t miss.
We approach each roof with clear communication, disciplined planning, and an unshakable commitment to excellence. Because when we say we’ll protect your home, we mean it—every task, every detail, every time.
Built to endure. Driven by pride. Rooted in Colorado. Led by purpose.