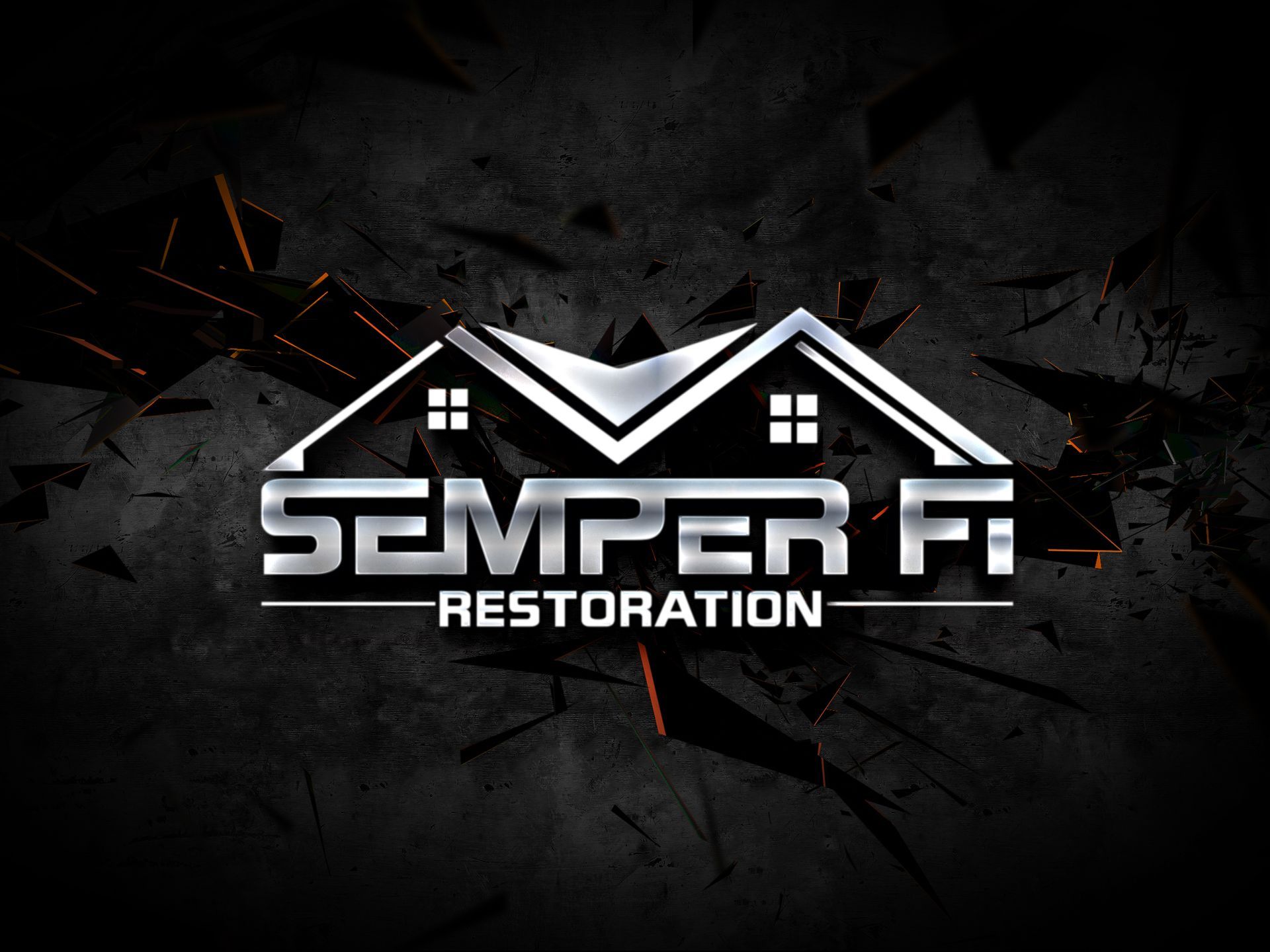
Roof Shingle Repair: DIY Steps, Costs, and When to Call Pros
One cracked or wind-flipped shingle can let a Colorado thunderstorm dump gallons of water onto your plywood deck, turning a quick $25 fix into a five-figure remodel. The good news: most homeowners can swap a handful of damaged asphalt shingles in an afternoon with basic tools and about $20–$150 in materials. The bad news: climb up there unprepared, and you risk emergency-room bills, voided warranties, and leaks that creep under the radar until mold blooms behind drywall.
This guide cuts through guesswork. You’ll learn how to spot trouble from the ground, price out repairs, gather the right gear, and install replacement shingles without damaging the rows around them. We’ll also flag the red-line scenarios—steep pitches, widespread hail bruising, sagging decking—where calling a licensed roofer like veteran-owned Semper Fi Restoration is the smartest and safest play. By the final section you’ll have a clear plan to protect your roof, your budget, and your peace of mind—whether you tackle the job yourself or hand it off to the pros. Ready to get started? Let’s secure those shingles before the next storm rolls across the Front Range.
Step 1: Evaluate Roof Damage and Personal Safety
Before you even think about prying up a shingle, get a clear picture of what you’re dealing with and whether it’s safe to leave the ground. A rushed, “looks-okay” inspection is how a $75 roof shingle repair turns into rotted decking, attic mold, and insurance headaches. Spend a few focused minutes on assessment now and you’ll save hours—plus maybe a hospital trip—later.
Inspect From the Ground Before Climbing
- Stand 30–40 ft away and scan the roof with binoculars or a drone. Look for lifted tabs, missing shingles, buckled lines, exposed nail heads, and piles of granules in the gutters.
- Step inside: stains on ceilings, damp insulation, or a musty attic smell all point to active leaks.
Conduct a Close-Up Roof Walk-Through
Set the ladder at a 4:1 angle, stabilize it, and climb only when the footing is solid. Starting at the eave, work upward one course at a time, photographing damage for insurance and chalk-marking questionable spots. Move slowly—rushing is how nearby shingles get cracked underfoot.
Distinguish Cosmetic vs. Structural Issues
Repairable on your own:
- A few cracked tabs
- Nail pops
- One or two missing shingles
- Light hail bruises
Call a pro:
- Soft or spongy decking
- Widespread granule loss
- Flashing failure at chimneys, valleys, or skylights
- Persistent attic moisture
Safety Precautions You Can’t Skip
- Weather window: dry, 40 °F–90 °F, winds under 10 mph.
- Gear up: non-skid boots, gloves, eye protection, and a 5,000 lb-rated fall-arrest harness.
- Always work with a buddy and keep kids, pets, and patio furniture clear of the drop zone.
Take these steps seriously; the rest of your roof shingle repair hinges on a safe, accurate evaluation.
Step 2: Calculate Repair Costs and Decide DIY or Hire
Sticker shock and surprise fees derail more weekend projects than any missing nail. Before you buy the first bundle of shingles, run the numbers. A clear budget will tell you whether a quick Saturday roof shingle repair is worth your time—or if calling in a crew makes better financial sense.
Average Price Ranges for Common Repairs
Most costs fall into three buckets: materials, labor, and incidentals (dump fees, permits). The table below shows ballpark figures for asphalt roofs in Colorado and similar markets:
Scope of Repair | DIY Materials | Typical Pro Invoice | What’s Included* |
---|---|---|---|
1–5 shingles | $75–$200 | $150–$400 | Shingles, nails, sealant |
Up to 1 bundle (≈20 shingles) | $150–$300 | $300–$800 | Materials + 1–2 labor hours |
Flashing + shingle section | N/A (specialty) | $400–$900 | New flashing, tear-off, disposal |
Valley or ridge cap patch | $120–$250 | $450–$1,000 | Ridge/valley shingles, caulk, cleanup |
*Add $25–$75 for a one-day dumpster bag; $50–$125 for city permits in some municipalities.
Hidden Expenses DIYers Often Miss
- Safety gear rentals: harness, roof jacks, ladder stabilizer ($40–$150).
- Tool purchases: magnetic nail sweeper, hook blades, caulk gun ($35–$60).
- Color mismatch if the shingle batch code differs—can ding resale value.
- Manufacturer warranty voids from incorrect nail placement or skipped underlayment.
- Medical bills: the average ER visit after a fall exceeds $3,000—far more than hiring a roofer.
Quick Decision Checklist: DIY or Professional
Run through these questions before committing:
- Is the roof pitch steeper than 6 ⁄ 12 or higher than one story?
- Has the roof already passed the 15-year mark or seen multiple patches?
- Do you have an active manufacturer or insurance warranty that requires licensed installation?
- Are you fully comfortable working at heights with power tools and a harness?
- Will weather give you at least 24 rain-free hours for sealant to cure?
If you answered “yes” to any of the first three—or “no” to the last two—hiring a licensed local contractor is usually the safer, cheaper long-term choice.
Step 3: Gather Materials, Tools, and Protective Gear
A successful roof shingle repair starts long before your boots touch the ladder rungs. Having every tool and material staged on-site keeps you off the roof fewer times and reduces the chance you’ll rush—or skip—a critical step. Do a single, organized hardware-store run, lay everything out on a tarp, and double-check quantities before climbing. The lists below assume you’re replacing a handful of three-tab or architectural asphalt shingles; scale up if you’re tackling a larger patch.
Essential Tool Kit
- Flat/pry bar for lifting tabs and popping nails
- Roofing hammer or pneumatic nail gun with 1¼–1½ in. galvanized nails
- Utility knife with hook blades (they glide through thick shingle mats)
- Chalk line for straight courses
- Caulk gun for sealant tubes
- Magnetic nail sweeper to keep stray metal out of tires and paws
Materials Checklist
- Matching asphalt shingles (buy a full bundle so color lots match)
- 1¼–1½ in. corrosion-resistant roofing nails
- Asphalt roof shingle repair sealant or plastic roofing cement
- Underlayment patch: 15-lb felt, synthetic underlayment, or ice-and-water membrane for valleys
- Optional: roofing repair tape for hairline cracks, pre-boxed shingle repair kit for small jobs
Safety & Site-Prep Equipment
- Extension ladder with stabilizer bar and leg levelers
- Roof jacks and a 2 × 10 plank if the pitch is 5/12 or steeper
- Personal fall-arrest system rated to 5,000 lb with rope grab and anchor
- Non-skid boots, cut-resistant gloves, safety glasses, and hard hat
- Heavy-duty tarp to shield landscaping and catch debris
Timing and Weather Conditions
- Block out 4–6 hours of daylight; avoid “just before dark” starts
- Forecast must show zero rain for at least 24 hours so sealant cures
- Ideal ambient temperature: 40 °F–90 °F; colder shingles may crack, overheated mats get gummy
- Wind below 10 mph—gusts make carrying bundles and handling nails hazardous
Stocking these items ahead of time means the only surprises during your roof shingle repair will be how quickly the job goes once everything is within arm’s reach.
Step 4: Remove the Damaged Shingle(s) Without Harming Nearby Rows
Slow is smooth, and smooth is fast. Ripping out a broken tab in a hurry almost always cracks the mated shingles above it, doubling your work. Treat this phase like minor surgery: isolate the problem, free up the surrounding tissue, then extract without cutting anything vital. Work from the top down so gravity is on your side and keep a cordless blower handy to clear grit as you go.
Loosen the Self-Seal Strips
Modern asphalt shingles have tar “seal-down” dots that bond courses together once the sun heats them. Pry too eagerly and you’ll tear the mat. Instead:
- Slide a flat bar under the lower edge of the shingle directly above the damaged one.
- Wiggle gently to break the adhesive, moving left to right until the entire tab lifts.
- On cold days (< 50 °F), warm the area with a heat gun set to low for 10–15 seconds—just enough to soften the tar without blistering the granules.
Extract Roofing Nails Carefully
The shingle you need to remove is still pinned by nails driven through the course above. Free those fasteners first:
- Locate nail heads by feel; they sit about 1 in. above the cut-out or, on architectural shingles, roughly 5 ⅝ in. from the bottom edge.
- Slip the pry bar under the nail head, lever up until the shank lifts ⅛ in., then roll the bar sideways to walk the nail out cleanly.
- Typical counts: 4–6 nails in standard wind zones, 6–8 along Colorado’s gusty Front Range. Remove every nail that pierces the damaged shingle—even the ones hiding under overlapping tabs—before trying to slide it out.
Slide Out and Dispose of the Damaged Shingle
With nails gone, grasp the shingle by the corners and pull downward. If it sticks:
- Use a hook blade to cut stubborn asphalt seams.
- Probe the exposed decking with a screwdriver; any soft or punky areas signal rot that must be addressed before replacement.
- Drop the shingle into a bucket instead of tossing it—loose debris can scar siding or plug gutters.
Prep the Repair Area
A good swap is only as strong as its foundation:
- Sweep away loose granules and dust so underlayment patches adhere.
- Bridge any torn felt or membrane with a 6-in. strip of 15-lb felt or ice-and-water shield; fasten with roofing cap nails.
- Confirm adjacent shingles still lie flat; re-seat any lifted corners with a dab of sealant.
- Finally, double-check the nail holes you backed out. If any penetrate the exposed deck, fill them with roof cement to keep future leaks at bay.
Take a breath—getting the teardown right sets you up for a seamless install in the next step.
Step 5: Install Replacement Shingles and Seal the Repair
With the damaged piece gone and the deck prepped, you’re past the halfway mark of your roof shingle repair. The goal now is simple: drop in a new shingle that lies dead-flat, nails tight, and sealant fully bonded so wind and water can’t tell the difference. Take your time here—most leaks start because fasteners were mis-placed or tabs were never re-sealed.
Position and Fasten the New Shingle
Slip the replacement under the course above, matching the butt edge and keyways to the adjacent shingles. If you’re working with architectural styles, dry-fit first and trim with a hook blade so the staggered pattern stays consistent.
- Drive galvanized roofing nails
1"
above the shingle cut-outs (or the manufacturer’s nailing line) and¾"
from each end. - Keep nails perpendicular to the deck and flush with, not cut into, the surface.
- High-wind zones like the Colorado Front Range demand six nails per shingle; follow local code or manufacturer specs.
Check alignment with a quick glance down the course—any uphill tilt will telegraph through every row above it.
Reseal Lifted Tabs for a Watertight Bond
The pry work in Step 4 broke the factory seal on surrounding shingles, so you need to re-activate it:
- Squeeze a pea-sized dab of asphalt roof sealant beneath every tab you lifted.
- Press the shingle down until the tar beds; wipe excess that oozes out.
- On cool days, set a brick or weighted pad over the area for 10–15 minutes to ensure adhesion.
Patch Minor Cracks or Torn Corners In-Place
Not every blemish warrants a full swap. For hairline splits or a corner nick:
- Clean away grit, then butter the underside of the crack with sealant.
- Press the mat flat and smear a thin topcoat over the seam.
- Harvest a pinch of granules from a spare shingle and sprinkle them onto the wet sealant—instant camouflage.
Perform a Leak-Check Before Leaving the Roof
Have a helper stand in the attic with a flashlight while you shower the repair area with a gentle garden hose, working from the ridge downward. Any drip, dark spot, or musty odor is your cue to add more sealant or re-set a nail right now, before sun-baked shingles make adjustments harder. Once the test runs dry, you’re ready to clean up and call this repair mission accomplished.
Step 6: Post-Repair Cleanup, Inspection, and Preventive Maintenance
The shingles are back in place, but you’re not done until the site is spotless and the work is documented. A five-minute sweep can keep nails out of tires, while a couple of photos could save you hours of warranty wrangling later. Treat this wrap-up phase as the insurance policy on your entire roof shingle repair.
Job-Site Cleanup
- Sweep loose granules off the roof so they don’t clog gutters.
- Run a magnetic nail sweeper over lawn, beds, and driveway—check twice near downspouts where nails collect.
- Flush gutters and downspouts with a garden hose to clear debris.
- Bag torn shingles and felt; dispose of them at a construction landfill (expect weight fees of $30–$50 per ton).
Document the Repair
- Snap “after” photos from the same angles you used for the damage shots.
- Staple receipts, serial numbers, and shingle batch codes to a copy of the photos.
- Log the repair date and scope in a home-maintenance file—handy for resale disclosures or future warranty claims.
Routine Maintenance to Extend Roof Life
- Inspect roof and attic every spring and fall; look for nail pops, lifted tabs, or new stains.
- Clean gutters and re-seal exposed flashings at chimneys, skylights, and valleys.
- Trim branches back at least 6 ft to reduce abrasion and leaf buildup.
- Ensure attic ventilation meets code (
1 sq ft
net free vent per300 sq ft
attic floor ) to prevent ice dams and heat-blistered shingles.
A tidy site, thorough records, and consistent upkeep will stretch the life of your recent repair and help you dodge bigger, costlier issues down the road.
Step 7: Know When to Call a Professional Roofer
Even the handiest homeowner hits a point where ladders, liability, and logistics tip the scales toward hiring help. The goal is to spot that moment early—before small roof shingle repair jobs snowball into full-blown replacements or interior water damage.
Red Flags That Require Expert Attention
- New ceiling stains or drips after every storm
- Hail bruising or granule loss across an entire slope
- Sagging decking, moldy attic insulation, or two layers of shingles already in place
- Work area near power lines or any roof pitch steeper than 6⁄12
If any box gets checked, step off the ladder and pick up the phone.
Why a Local Licensed Contractor Often Saves Money
A seasoned crew arrives with harnesses, compressors, and code know-how. That efficiency means:
- Faster dry-in during sudden Colorado weather swings
- Access to manufacturer-trained installers and extended material warranties
- Proper documentation for insurance claims—often netting you more reimbursement than the repair costs
National Chains vs. Local Specialists: Who Serves You Better?
Out-of-state “storm chasers” may vanish after the check clears. Local outfits like veteran-owned Semper Fi Restoration stick around to honor warranties, offer free assessments, and recommend impact-rated shingles built for Front Range wind gusts.
How to Vet a Roofer Before You Sign
- Verify Colorado license, general liability, and workers’ comp.
- Request three recent local references plus manufacturer certifications (GAF, Owens Corning).
- Demand a written estimate detailing scope, materials, timeline, and cleanup plan.
- Confirm the contract includes both workmanship and transferable material warranties.
Follow these steps and you’ll trade guesswork for guaranteed workmanship—no ER visits required.
Keep Your Roof in Top Shape
Stay proactive and you’ll spend far less time (and money) on emergency roof shingle repair. A few seasonal check-ins and smart habits go a long way toward keeping water where it belongs—outside.
- Inspect the roof and attic twice a year, plus after major hail or wind events
- Budget realistic DIY vs. pro costs before buying materials
- Gather tools, safety gear, and weather intel ahead of climbing
- Remove damaged shingles slowly to protect surrounding courses
- Install replacements with correct nail spacing and fresh sealant
- Hose-test your work and photograph the finished patch
- Clean the site, sweep for nails, and file receipts
- Schedule professional help for steep pitches, widespread damage, or active leaks
Need a second set of eyes? Colorado homeowners can book a free, no-pressure roof assessment with the veteran-owned team at Semper Fi Restoration. We’ll spot problems early and give you an honest plan—whether that’s a quick patch or a full upgrade to storm-tough shingles.
Our Mission
At Semper Fi Restoration, our mission is unwavering:
To defend homes, uphold integrity, and execute every project with the discipline, precision, and relentless commitment that defines us as a veteran-owned, Marine Corps–inspired company.
From Lakewood to Longmont, from Thornton to Sedalia, we serve the communities we call home. These aren’t just job sites—they’re neighborhoods where we’ve shaken hands, climbed ladders, earned trust, and protected families.
We don’t just repair roofs—we defend homes and safeguard peace of mind.
In a region where hail, wind, and unpredictable weather strike hard, we hold the line where it matters most—your rooftop. In an industry full of shortcuts and quick-fix promises, we remain grounded in principles: discipline, precision, and purpose.
Our crews operate with the rigor of a military unit—organized, reliable, and mission-focused. We are selective in who we bring onto our team, because every person represents our name, and every nail we drive carries our reputation.
We don’t cut corners. We don’t accept mediocrity.
Accountability is our foundation. We demand it from ourselves and deliver it to our clients. From Commerce City to Erie, every inspection, every estimate, and every completed job is a reflection of the standards we refuse to lower.
Every project is a mission. And we don’t miss.
We approach each roof with clear communication, disciplined planning, and an unshakable commitment to excellence. Because when we say we’ll protect your home, we mean it—every task, every detail, every time.
Built to endure. Driven by pride. Rooted in Colorado. Led by purpose.